Do you recall when “tariffs” was a dull term politicians tossed around as we changed the channel? It’s coming a little closer to home, your garage, your assembly line, and perhaps even your paycheck. The U.S. tariffs on Canadian automotive exports have triggered a full-throttle chain reaction, slamming brakes of jobs, exports, innovation, and supply chains. These are 20 shocking impacts of U.S. tariffs on Canadian auto jobs:
Ripple Effects Across the Border: Why U.S. Tariffs Hurt Canada Too
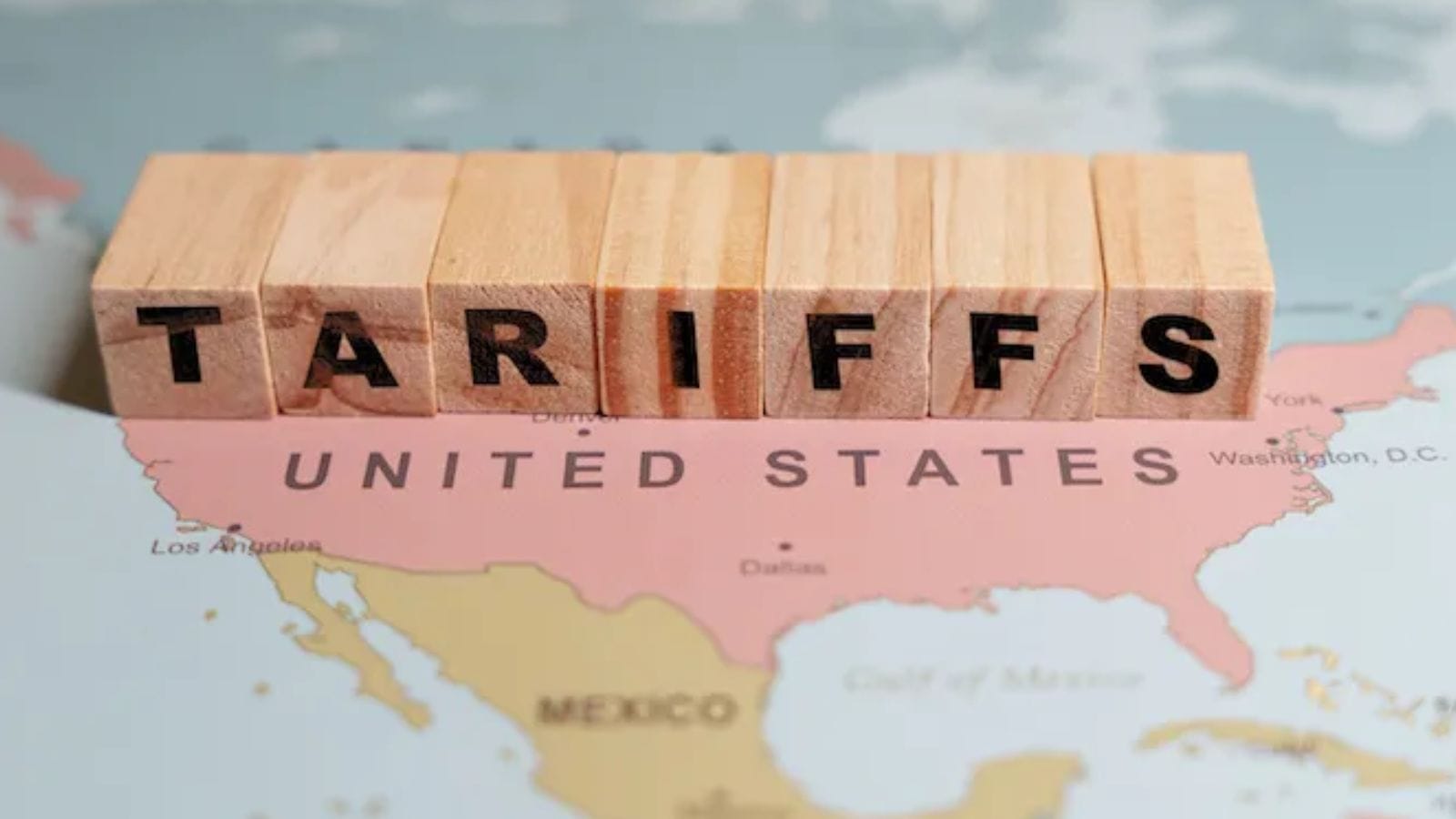
The U.S. and Canadian auto industries are like conjoined twins. Tariffs by the U.S. have created ripple effects that resonate across the border and shatter a trade relationship worth more than $110 billion annually. When U.S. tariffs raise the price of Canadian-made vehicles and auto parts, it damages profits and erodes the pillars of Canada’s export economy. Exports of Canadian vehicles fell 9% last quarter after tariffs were in place. An estimated 150,000 Canadian workers, including assemblers, engineers, logistics, and even cafeteria workers in auto factories, could be at risk in the next two years. It’s a domino effect that’s just getting underway.
The Parts Problem: Supply Chain Chaos in Canadian Factories
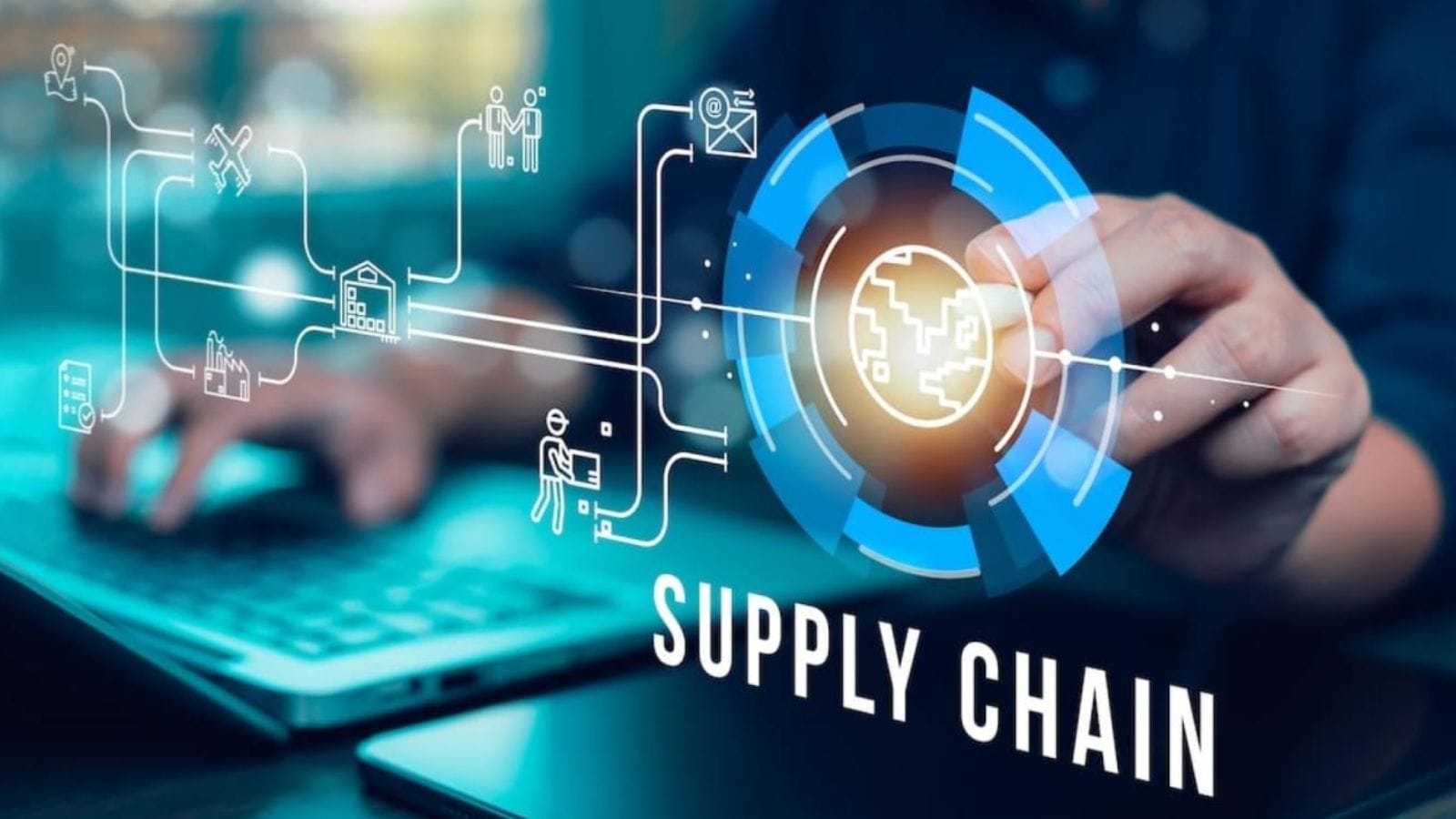
Imagine constructing a car and discovering that each third component became more expensive, postponed, or out of stock. That’s the case for Canadian motor vehicle producers. Auto part production constitutes a large majority of Canada’s industry exports, but the 25% tariff on essential parts has increased costs dramatically. On average, the price of parts per unit has increased by $600–$900. This inflation disproportionately affects Ontario and Quebec factories with the most severe production slowdowns and expensive purchases from other markets. Once a 72-hour just-in-time delivery process, it’s taking over a week and disrupting production cycles. Close to 18% of small and medium-sized parts suppliers say they’re on the verge of closure. The typical car consists of roughly 30,000 pieces; Canadian plants normally bring in 40% of them from America.
Layoffs on the Line: Thousands of Jobs Hanging by a Thread
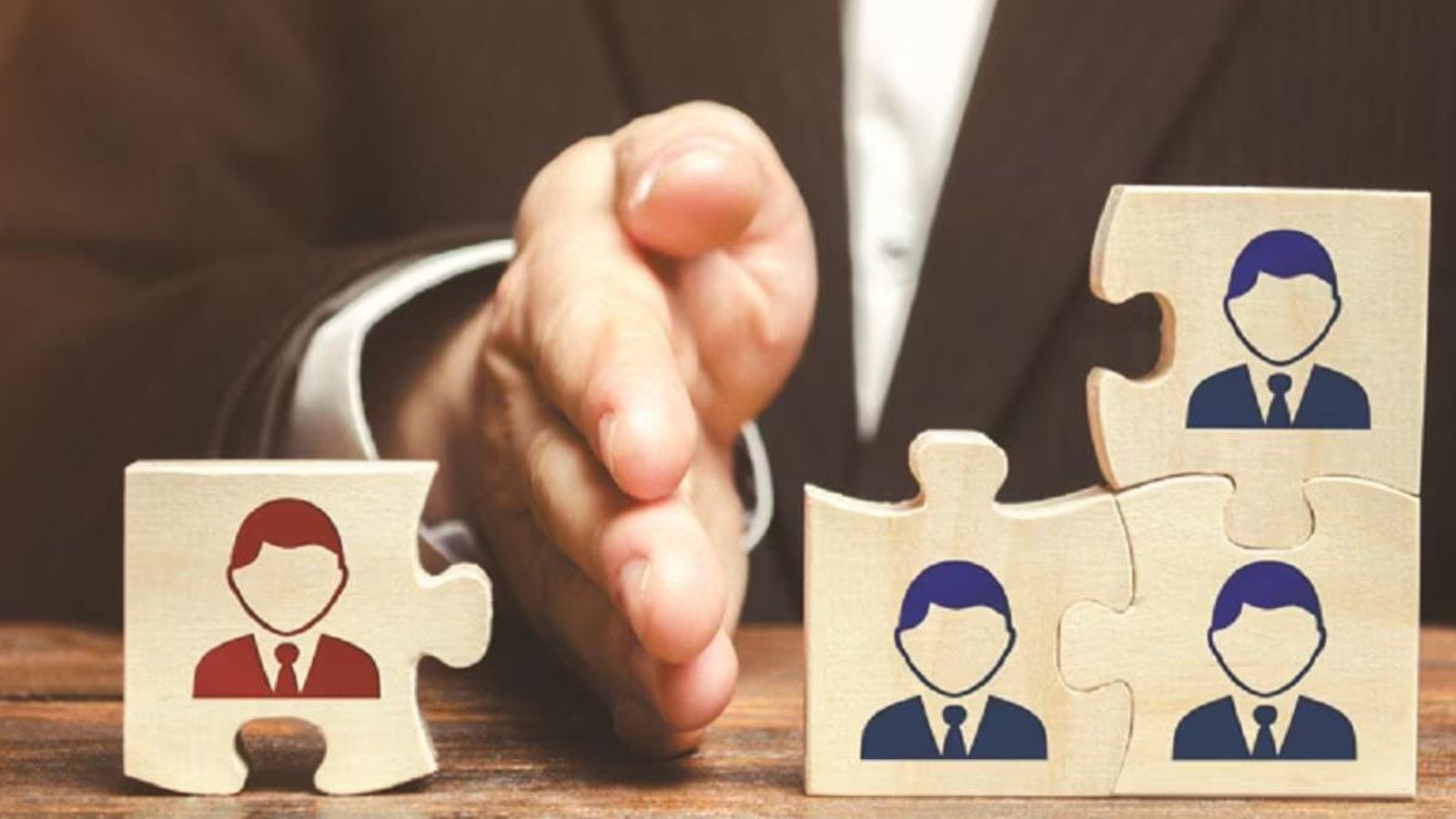
Tariffs rattle the economy and devastate the workforce head-on. In Canada’s automotive industry, layoffs have already become a bitter truth. Within three months under new U.S. tariffs, more than 6,000 employees were temporarily or permanently laid off. Ontario city assembly lines in Oshawa and Windsor were shut down, affecting wages and livelihoods. Projections indicate that if tariffs continue for another 12 months, as many as 28,000 more jobs might be lost, primarily line workers, toolmakers, and logistics coordinators. The automotive sector does not exist in a vacuum, and each lost job resonates through local economies. Restaurants, gas stations, and even daycare facilities feel the economic chill of every pink slip. For each auto assembly job, a minimum of seven other jobs are indirectly created in Canada.
Uncertainty in Windsor: The Auto Capital Feeling the Heat
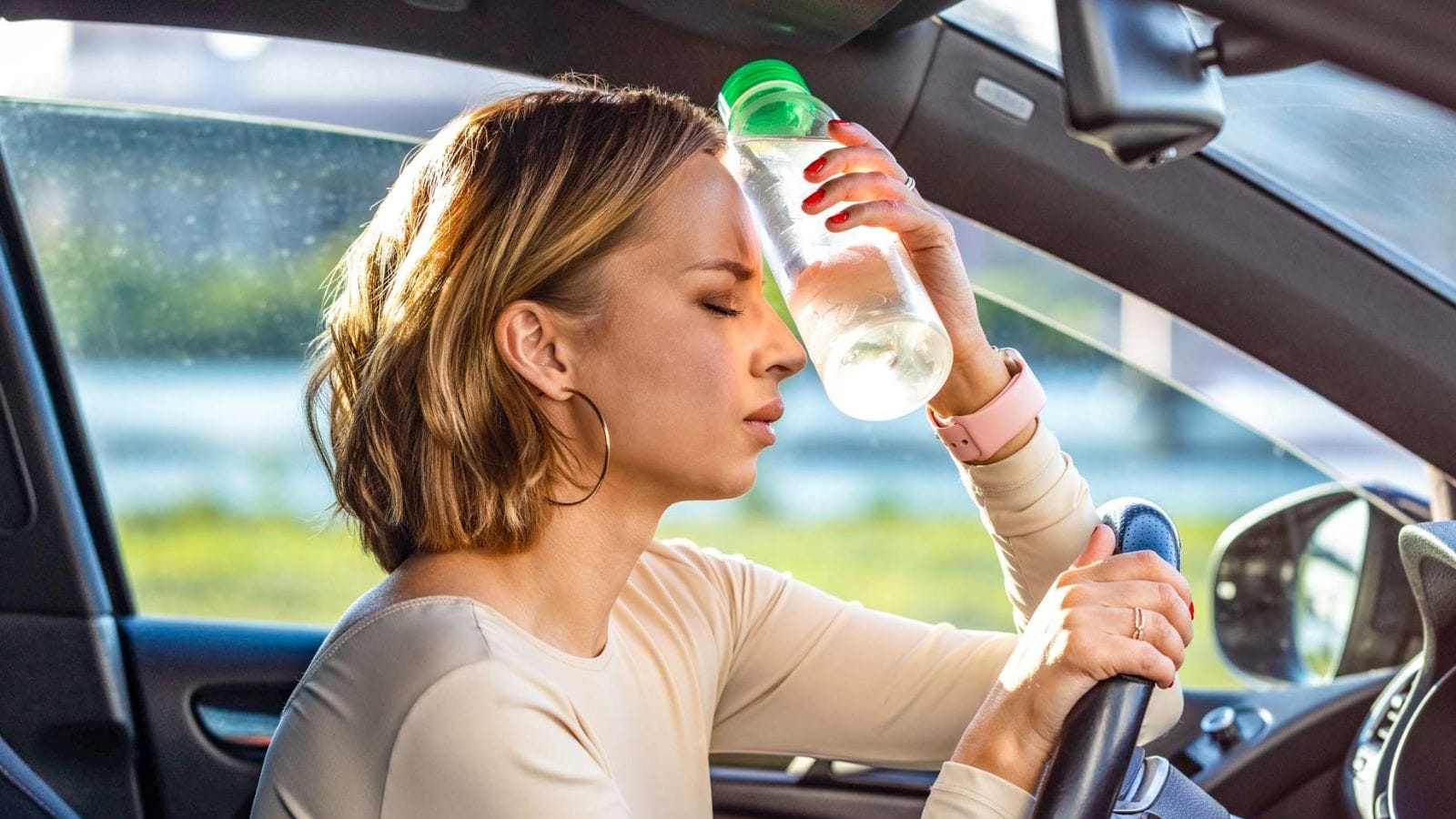
Windsor, generally called Canada’s Motor City, is tightening its belt with the squeeze. Over 30% of its labor is directly related to auto production, which exposes it to external shocks such as tariffs. The recent shutdown at flagship plants due to cost overruns and postponed parts has concerned residents about their economic futures. Windsor’s unemployment rate increased by 1.6% in 60 days following the tariff, and small business revenue fell 11% across the city. Tax revenues are declining, and plans for city growth are being put on ice or abandoned altogether. Windsor’s once-proud manufacturing base now teeters on unsteady ground.
U.S. Buyers Back Off: Slowing Demand for Canadian-Made Vehicles
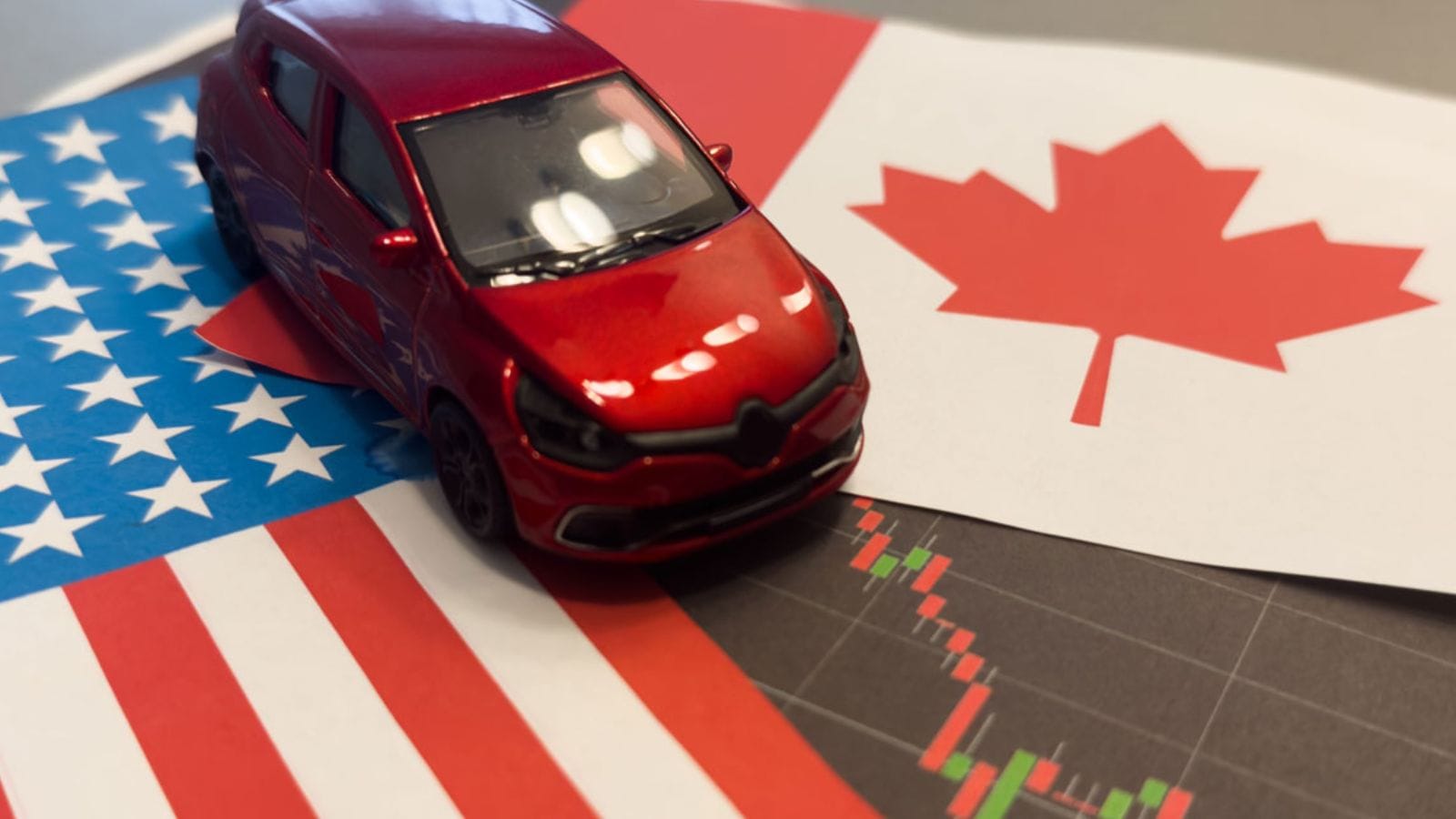
With Canadian vehicles tagged with increased import prices, American buyers are reconsidering. Sales of Canadian-built vehicles in the United States declined by 13% in the first quarter after tariffs were imposed as the added costs trickled down, and a competitive $32,000 sedan costs nearly $38,000 upon crossing the border. Dealerships show increasing inventory and decreasing turnover, and orders are starting to be canceled for carmakers, which translates to reduced revenue and increased uncertainty. Approximately 72% of Canada’s vehicle exports are destined for the U.S., and a minor blow to demand can have a big impact.
Cost Overload: Why Canadian Cars Are Getting More Expensive
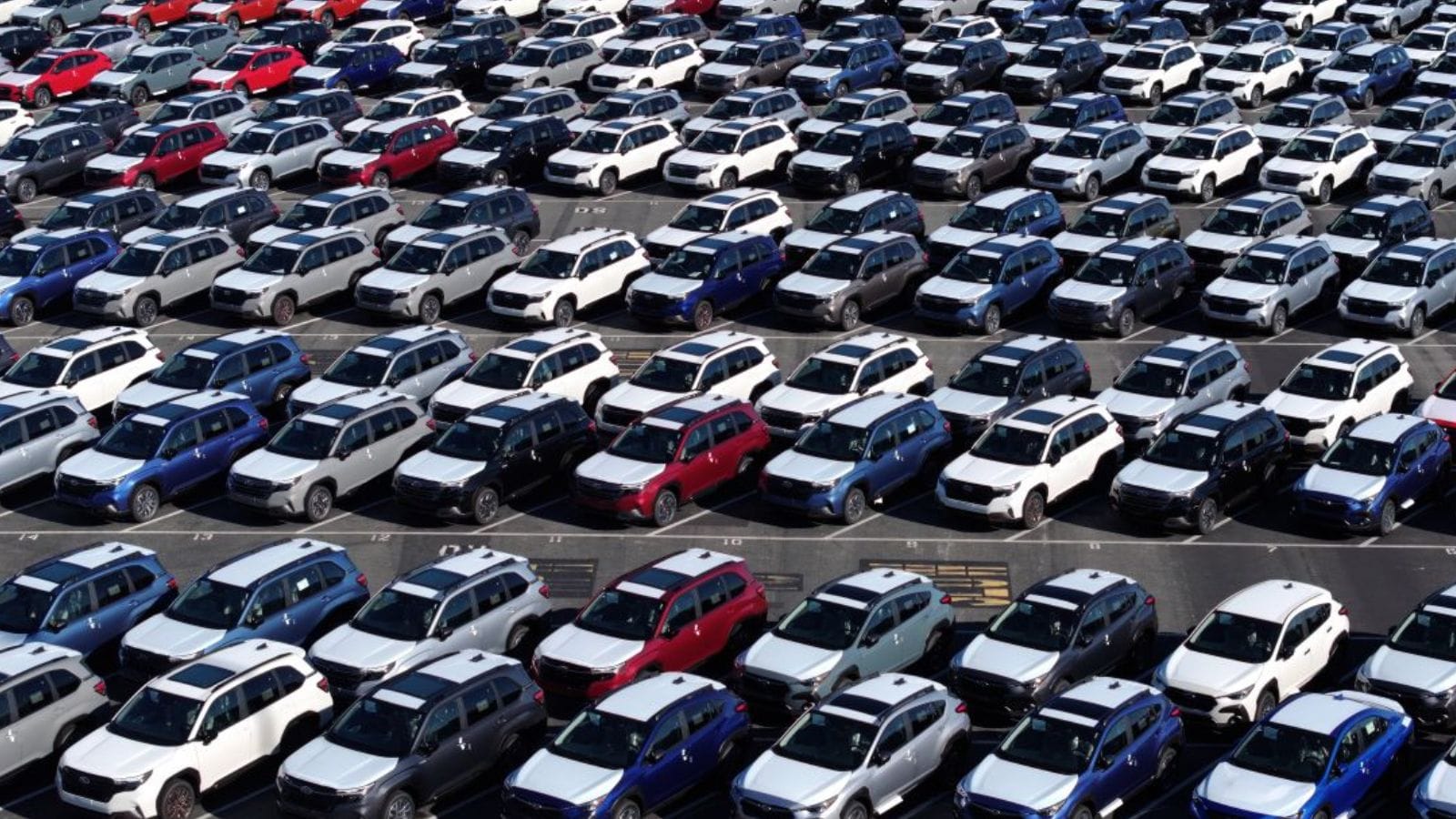
Tariffs don’t live in a vacuum. Instead, they compound. When you compound border taxes, rising shipping costs, and higher raw material costs, you have a nasty financial cake that nobody wants to eat. In just six months, the average production cost per vehicle in Canada has risen by $1,200. This encompasses the tariff, administrative hold-ups, and storage charges resulting from customs congestion. Consequently, cars made in Canada are losing competitiveness on the global stage, not just in the United States. Increased MSRPs are compelling consumers to buy used automobiles or those from untariffed nations. Auto manufacturers find it challenging to absorb costs without cutting margins or freezing worker bonuses. Car manufacturers typically profit less than 7% on a new vehicle, so even small cost increases can be detrimental.
Plant Closures on the Horizon: Might Your Hometown Be Next?
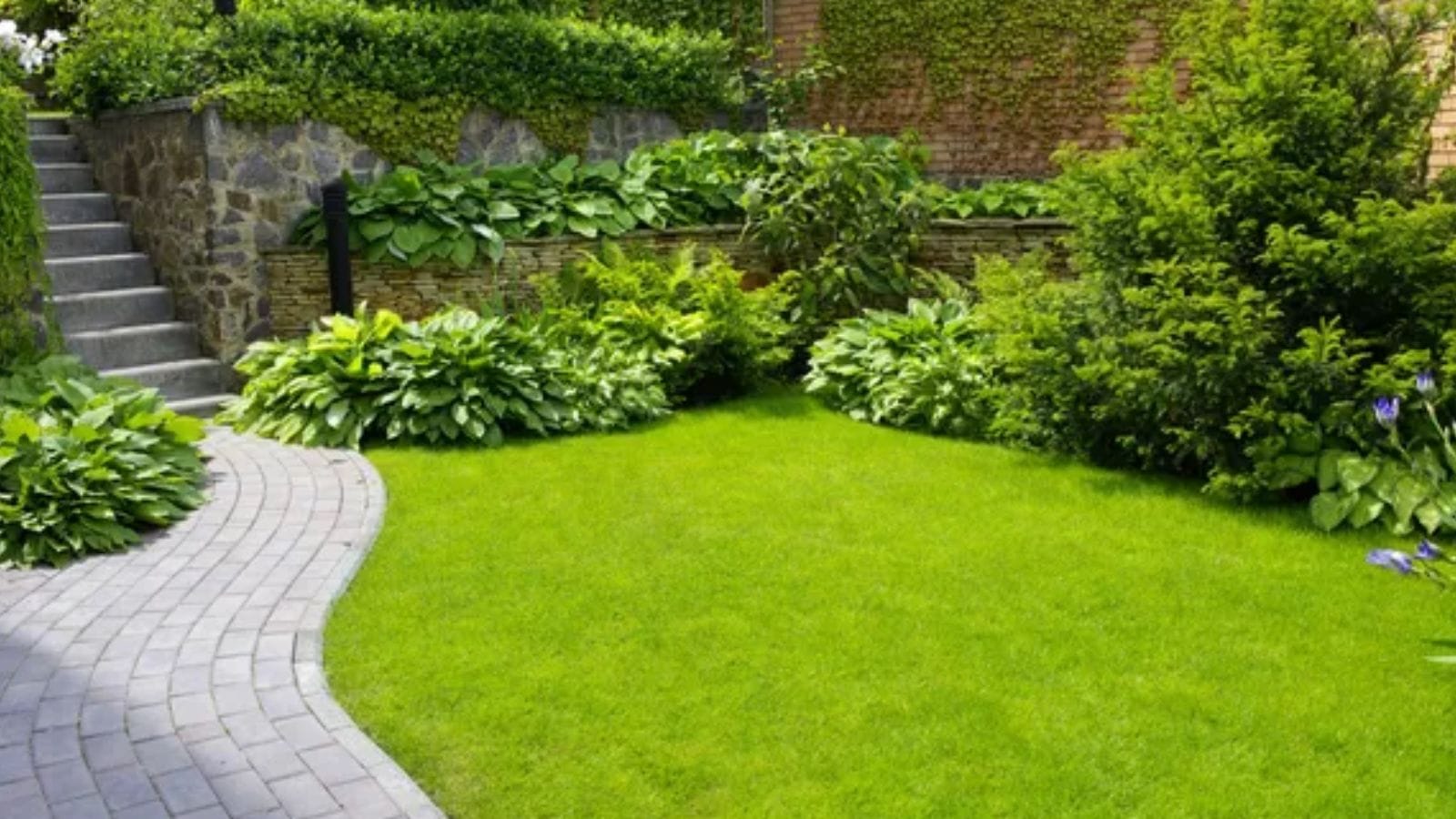
With a 14% decline in export volumes and high overheads, producers are reassessing their operations and considering closures. Three large auto plants said they would cut shifts or close outright. A fourth Brampton plant is “under strategic review,” a phrase that often conveys a less-than-positive impression. Another 5–7 plants may experience partial closures if tariff pressures persist within 18 months. These shutdowns destroy whole community systems. Cities constructed around a factory often experience real estate busts, dwindling school budgets, and a decline in local spirits. An average auto factory employs over 3,000 workers and indirectly supports an additional 9,000 jobs in the surrounding area.
Skilled Workers Scrambling: The Talent Drain Begins
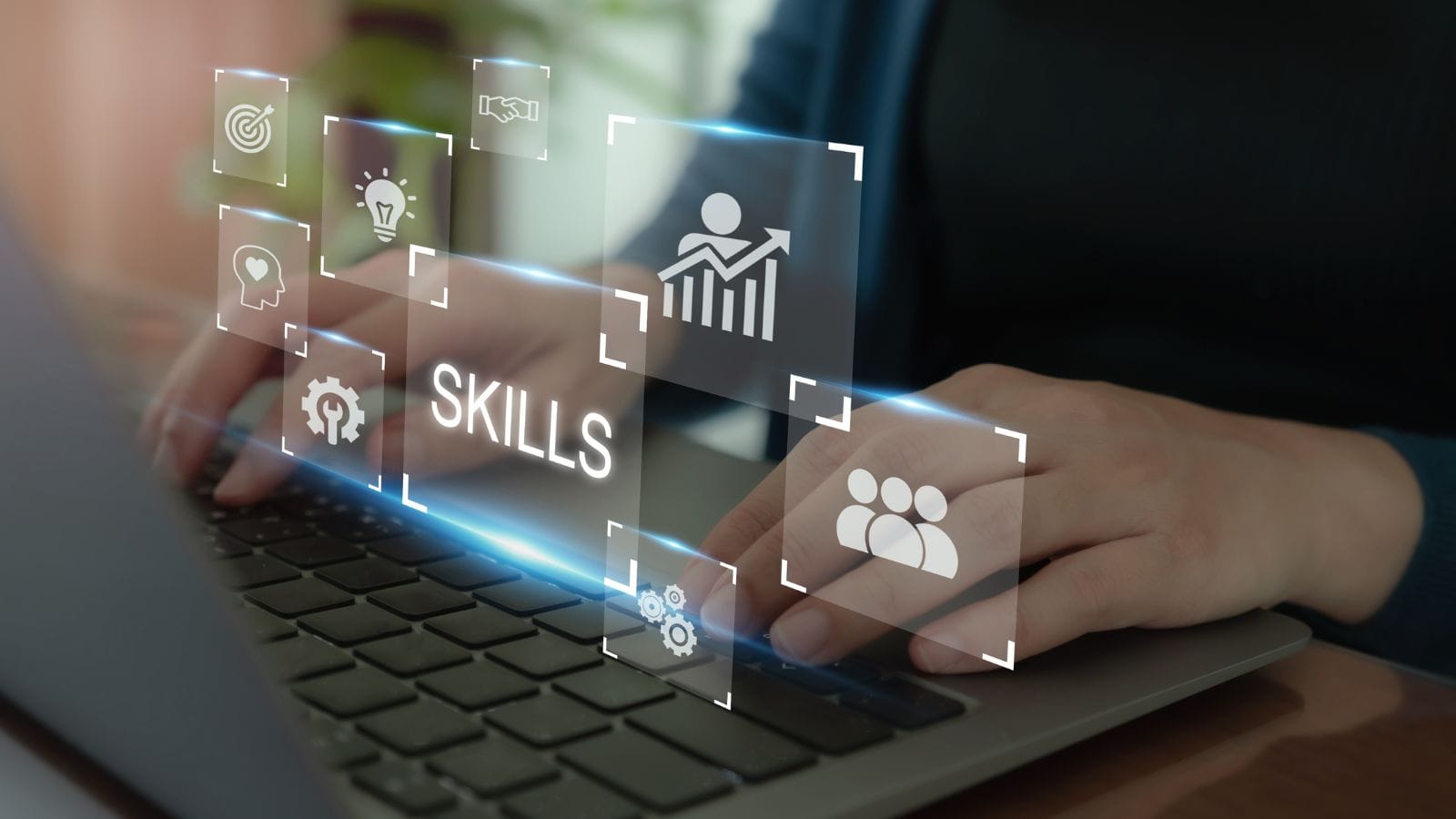
Canada has invested well in developing a skilled auto workforce, which includes engineers, designers, welders, and robotics specialists. But with plants idling and job security waning, many are abandoning ship. Over the last six months alone, technical schools have reported a 22% decline in enrollment in automobile-related courses. At the same time, employment boards indicate that listings for skilled labor outside the automotive industry, such as aerospace and technology, are on the rise. Skilled workers are the backbone of the business, and it’s not easy to bring them back once they’re gone. This brain and brawn drain erodes Canada’s capacity to innovate or shift to new technologies, such as electric and driverless cars. It takes 6–8 years to properly train the average auto worker in Canada for high-skill manufacturing work.
Union Uproar: Labour Leaders Sound the Alarm
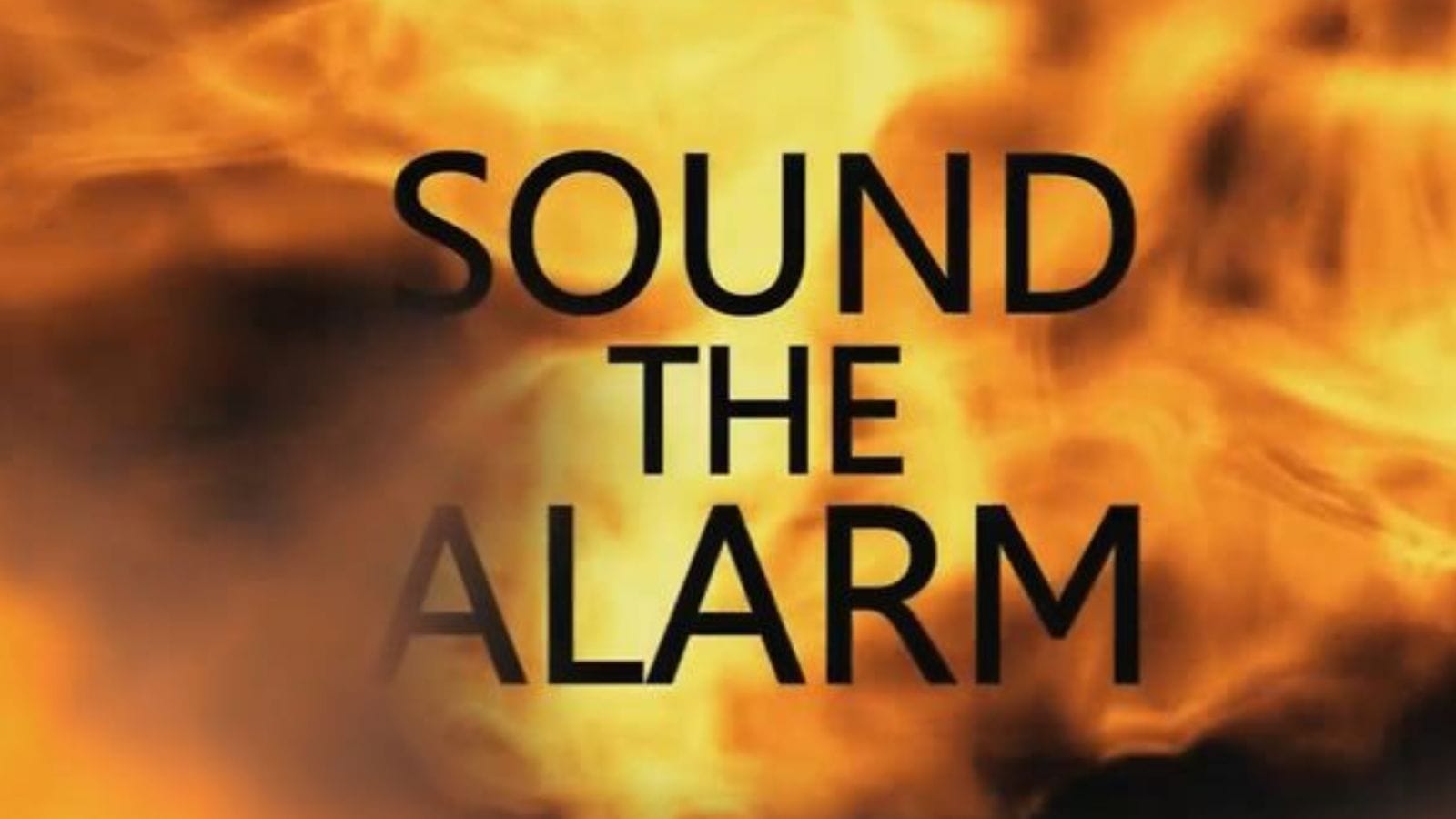
Tariffs rattled corporate boardrooms and set off union firestorms. Labor unions label the effect “economic sabotage,” referring to the violation of employment security agreements and a lack of government action. Over the last two quarters, union activity has jumped by 34%, with protests, negotiations, and even threatened strikes. Employees are seeking pay packages, tariff refunds, and employment guarantees. Some factories have gone to arbitration to settle issues directly prompted by layoffs and reduced hours. The conflict between automakers and unions is escalating, and continued turmoil may delay product launches or investment in new technologies, potentially putting Canada at a disadvantage in the international race for innovation.
Investment Freeze: Automakers Putting Projects on Hold
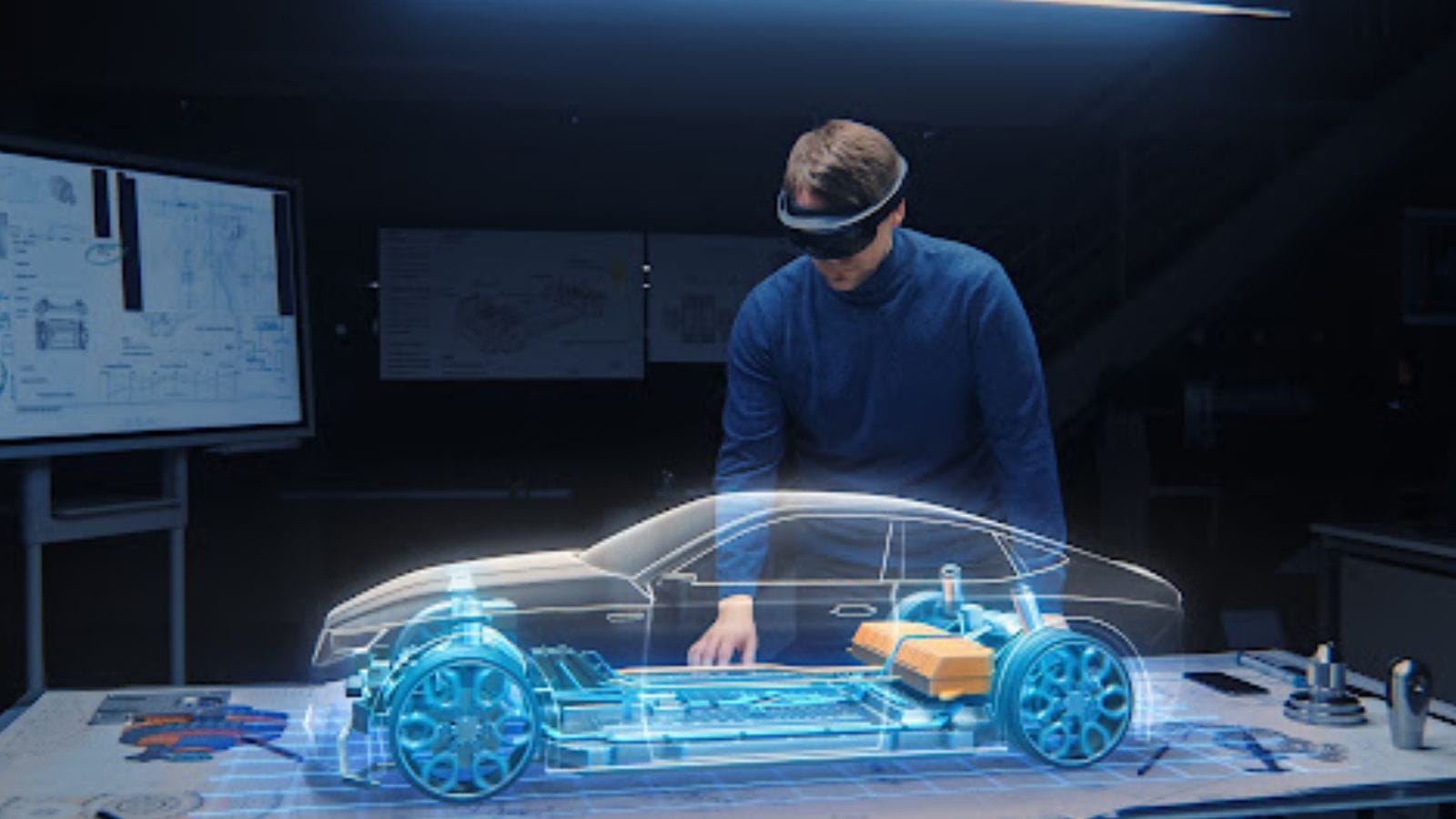
New investments are the lifeblood of any industry. But in today’s environment, automakers are putting Canadian projects on ice. At least five large expansion plans have been put on hold or terminated since tariffs were implemented. These involve EV production lines, battery plant expansions, and AI factory automation systems as investor confidence plummets. If business costs increase without a guaranteed return, companies invest elsewhere, often south of the border, where subsidies or incentives provide greater certainty. Slow investments result in fewer jobs, slower technological advancements, and eroded economic strength in major regions. Investing in an EV battery factory can generate over $5 billion for an economy and create more than 2,000 new jobs.
Export Nightmare: How Red Tape is Delaying Deliveries
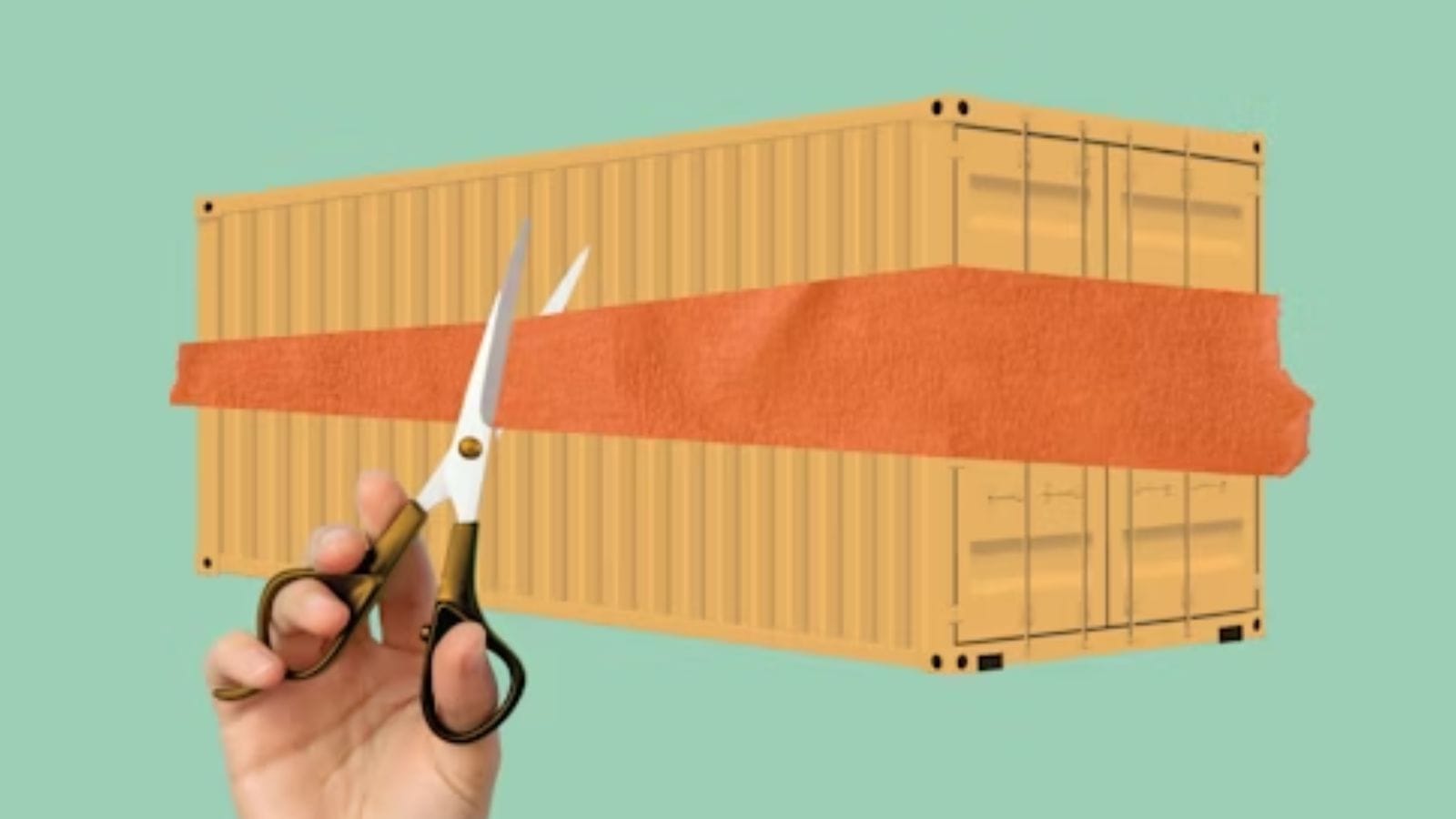
Tariffs increase costs and paperwork. With new compliance rules and customs checks, exporting vehicles and parts from Canada to the United States has become a complex bureaucratic process. Before tariffs, the average export clearance time was under 48 hours. Now, it’s over 96 hours. Every hour of delay costs money for warehousing fees, missed delivery slots, overtime pay, and lost customer trust. Exporters put the cost of each delayed shipment at an additional $1,000–$2,000 per vehicle in total logistics. Worse still, time-sensitive exports such as electric battery packs are experiencing cancellation rates through the roof. This red tape could be the last straw for manufacturers operating on razor-thin margins. More than 85% of Canadian car exports are to the U.S., so any delay is a national-scale issue.
Smaller Suppliers Squeezed Out: The Forgotten Victims
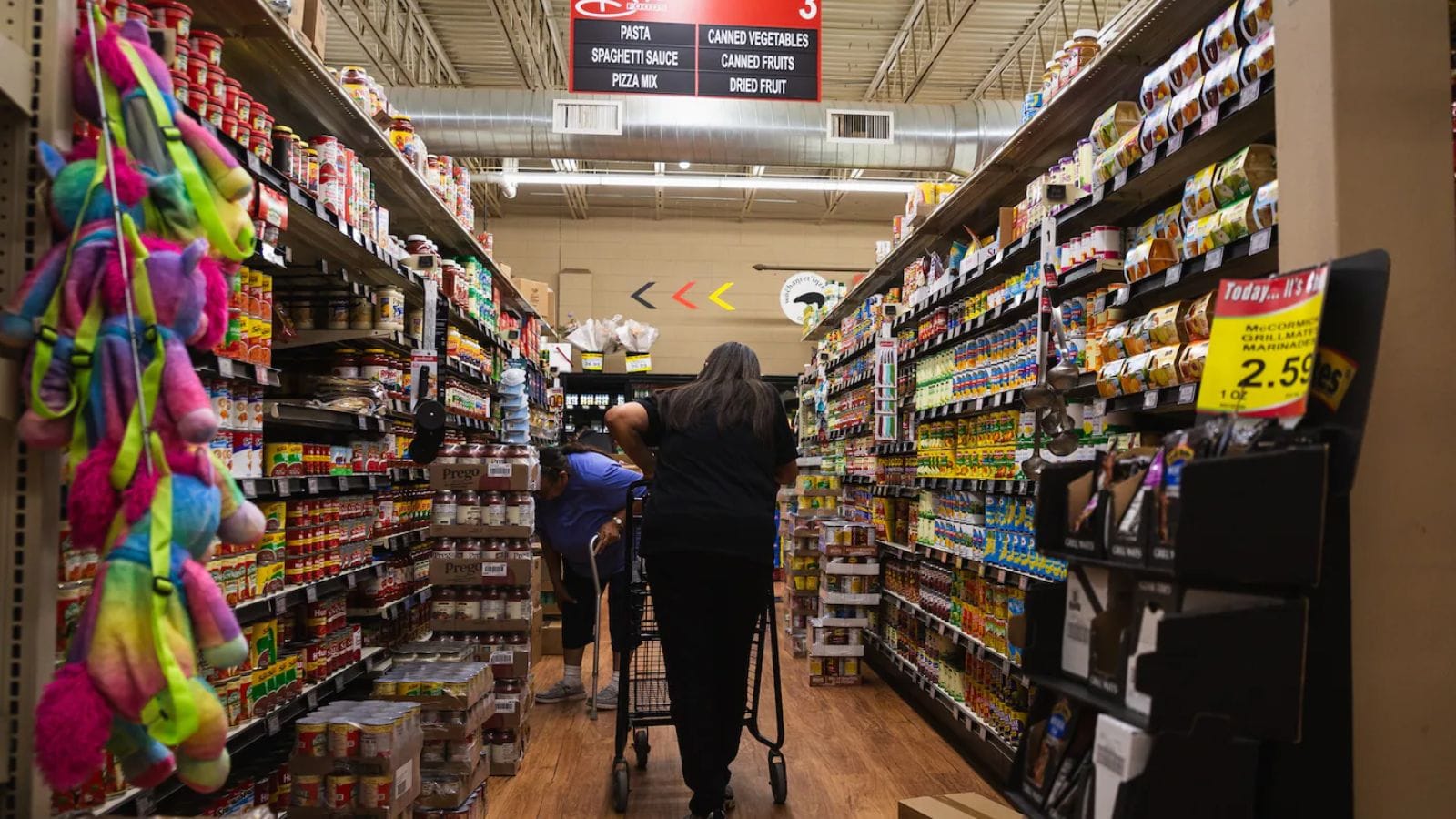
While giant auto manufacturers weather tariff storms with lawyers and worldwide supply chains, smaller suppliers teeter on the brink of extinction. Canada is home to more than 600 Tier 2 and Tier 3 suppliers, many of which are family-operated, that deliver niche parts ranging from gaskets to semiconductors. As tariffs increase input costs by 22% and delivery lead times double, most suppliers are being sliced from contracts. Already, 14% have either closed down or bankrupted over the past year. Those still running face margins under 3%, and most are too short of money to diversify to new clients or markets, resulting in a gradual bleed-out of the very lifeblood of Canadian manufacturing.
R&D Retreat: Innovation Takes a Backseat
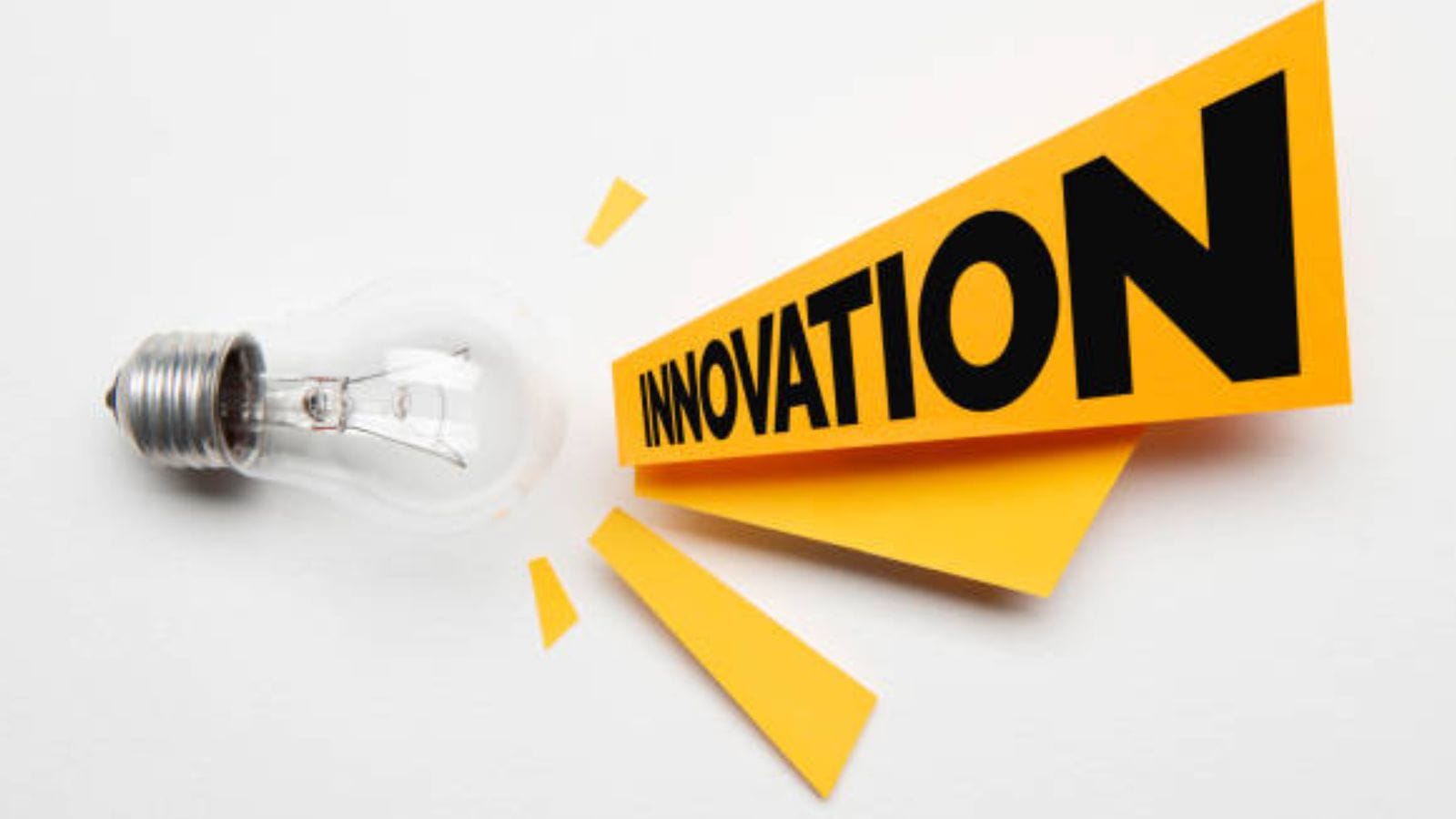
Innovation flourishes instability, and tariffs are the antithesis. As the financial squeeze tightens, Canadian automakers are reducing their research and development expenses to survive. R&D expenditures in the automotive industry in Canada fell 18% over the last fiscal year, ending a decade-long growth streak. EV propulsion systems, autonomous driving technology, and AI diagnostic projects are being put on hold or suspended indefinitely. Engineers are being diverted from innovation teams to cost-saving initiatives. This R&D pullback undermines Canada’s competitiveness in the next-gen auto world and threatens to fall behind global rivals. Once innovation stops, it takes years to regain lost ground.
Price Wars: Canadian Dealers Caught in the Crossfire
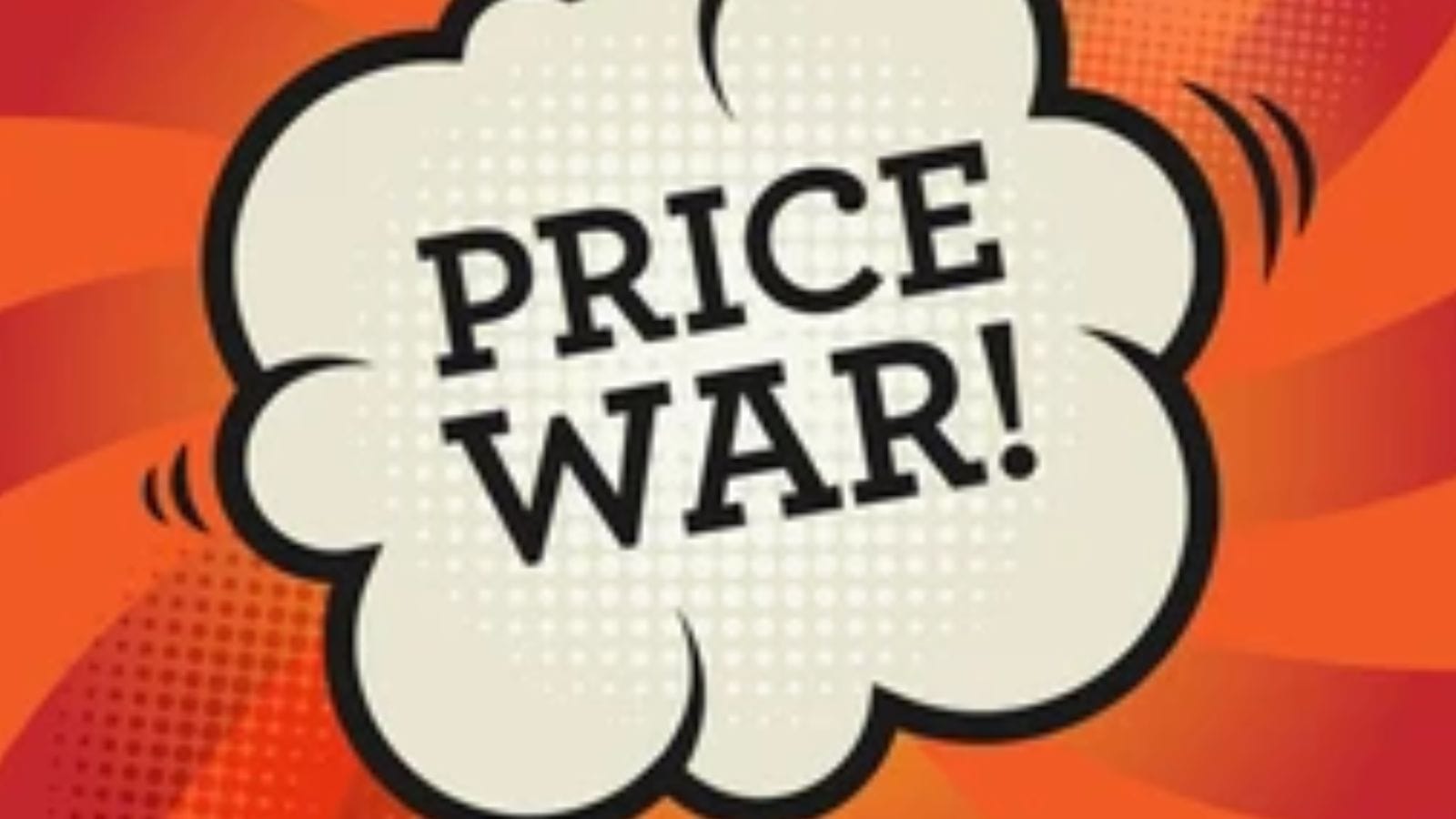
Dealerships are usually the forgotten intermediaries of trade wars but are also hurt. With cars costing more due to tariffs and inventory selling more slowly, Canadian dealers are cutting prices to move vehicles off their lots. This has sparked a Canada-wide price war, with some dealers slashing their profits by 30–40% to remain competitive. Sales volume is down 11% overall, and service revenue is declining as fewer new customers are arriving for maintenance packages. Dealer associations indicate that at least 9% of showrooms plan to close permanently by year-end if conditions fail to stabilize. The average Canadian dealership employs 40 people and generates over $60 million in annual sales, until tariffs disrupt the math.
Manufacturing Migration: U.S. Relocation in the Crosshairs
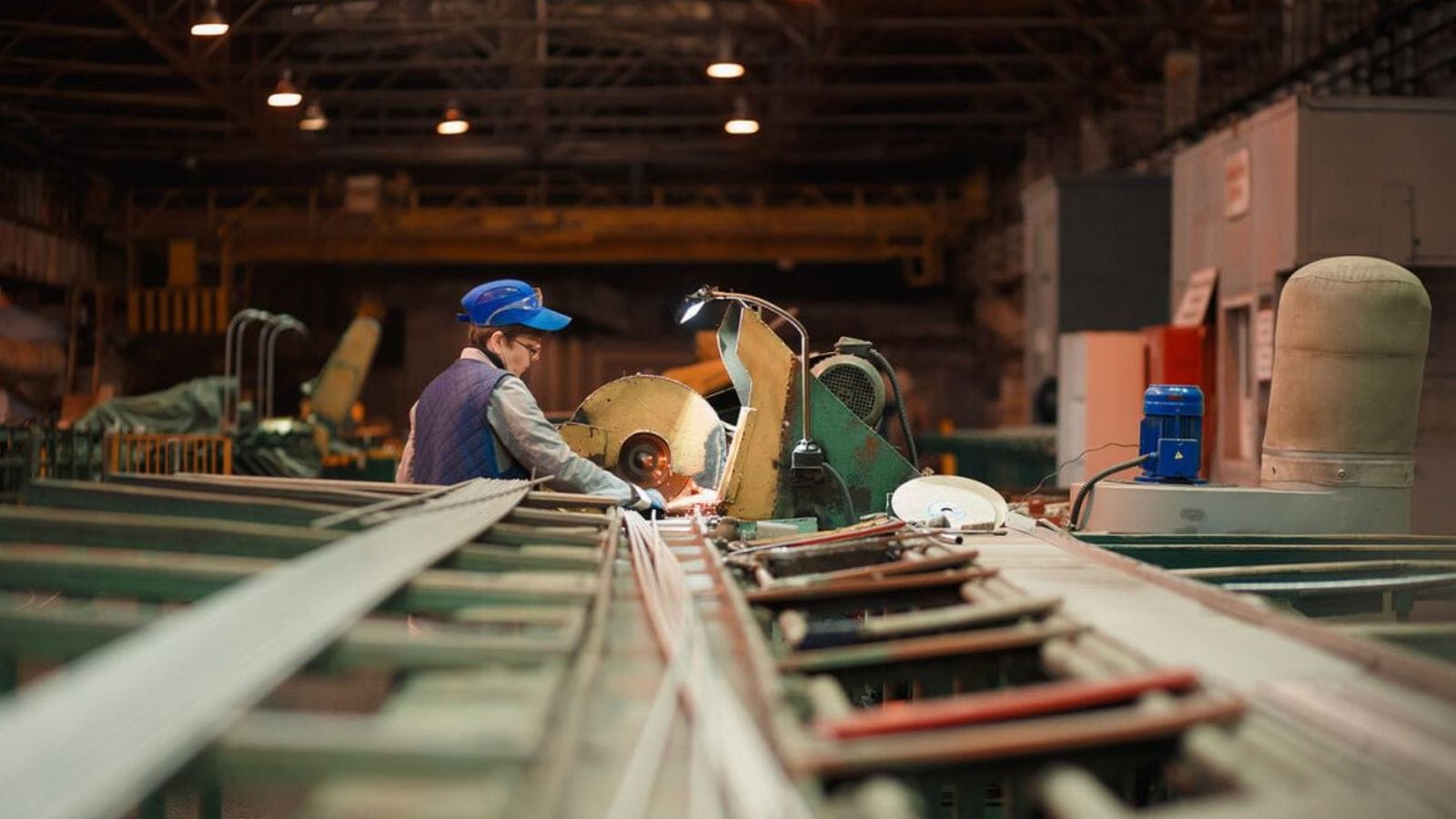
With costs rising and uncertainty looming, many firms are considering relocating their operations to the very nation that’s levying the tariffs. At least four large suppliers announced moves to facilities in the United States over the past year to skirt border expenses. Polls indicate that 22% of Canada’s auto companies actively pursue American expansion or relocation. States that provide tax incentives, tariff havens, and labor inducements make the transition financially attractive. This migration risks gutting Canada’s industrial base, especially in Ontario, where 90% of automobile manufacturing is concentrated. Each plant that relocates means lost jobs, experience, and community stability.
Job Retention Incentives: Are They Enough?
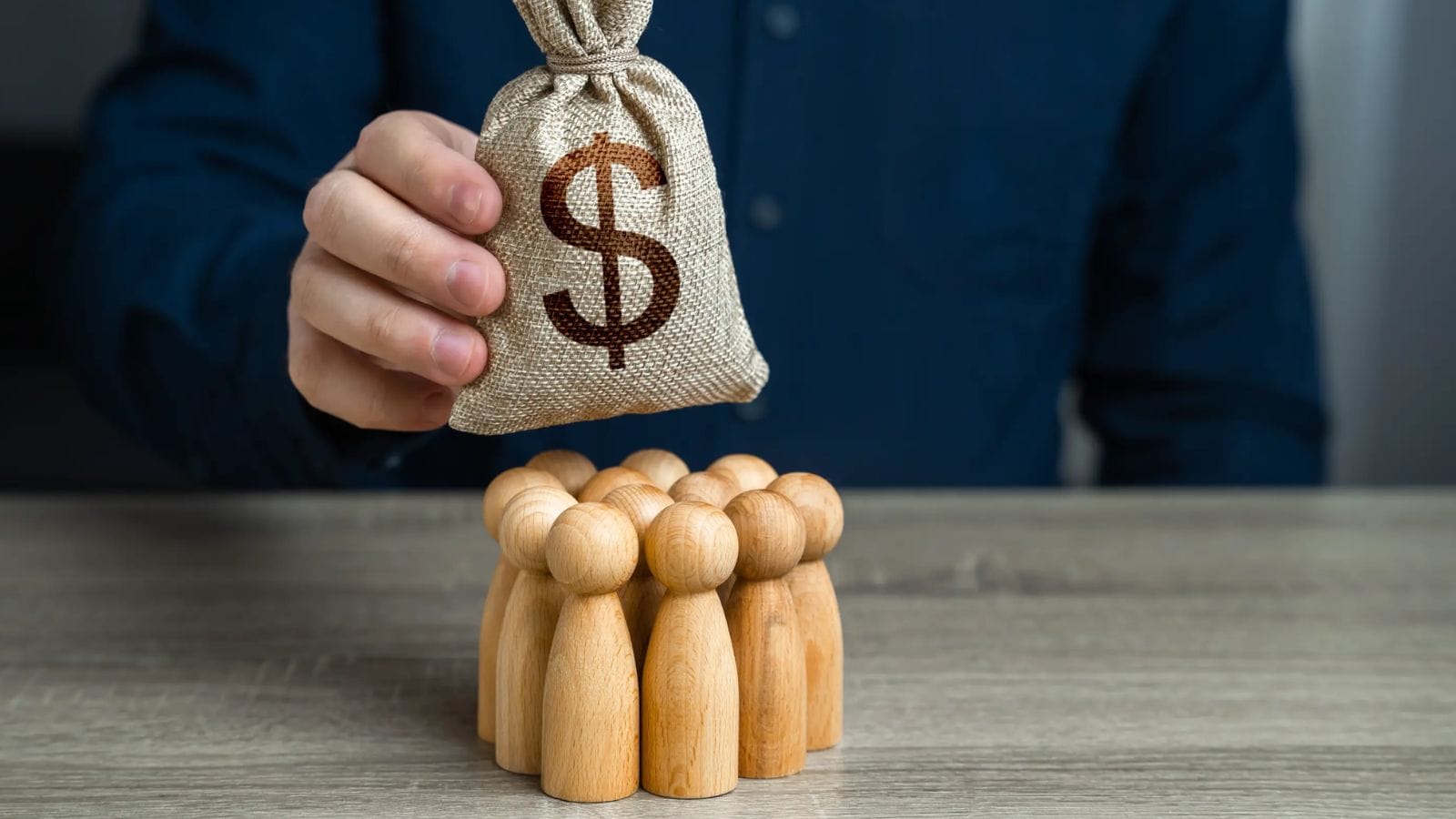
Since layoffs and factory closings have prompted Canadian provinces to introduce job retention incentives, from wage subsidies to tax credits, the evidence of their performance is unenthusiastic. Only 38% of manufacturers eligible to participate have sought them out, complaining of excessive red tape or inadequate coverage. While programs promise to save 20,000 jobs, economists caution they will only temporarily forestall inevitable cuts. Employers say that even with incentives, production inefficiencies and market contractions continue to render job retention financially unfeasible.
Impact on Canadian Electric Vehicle Production
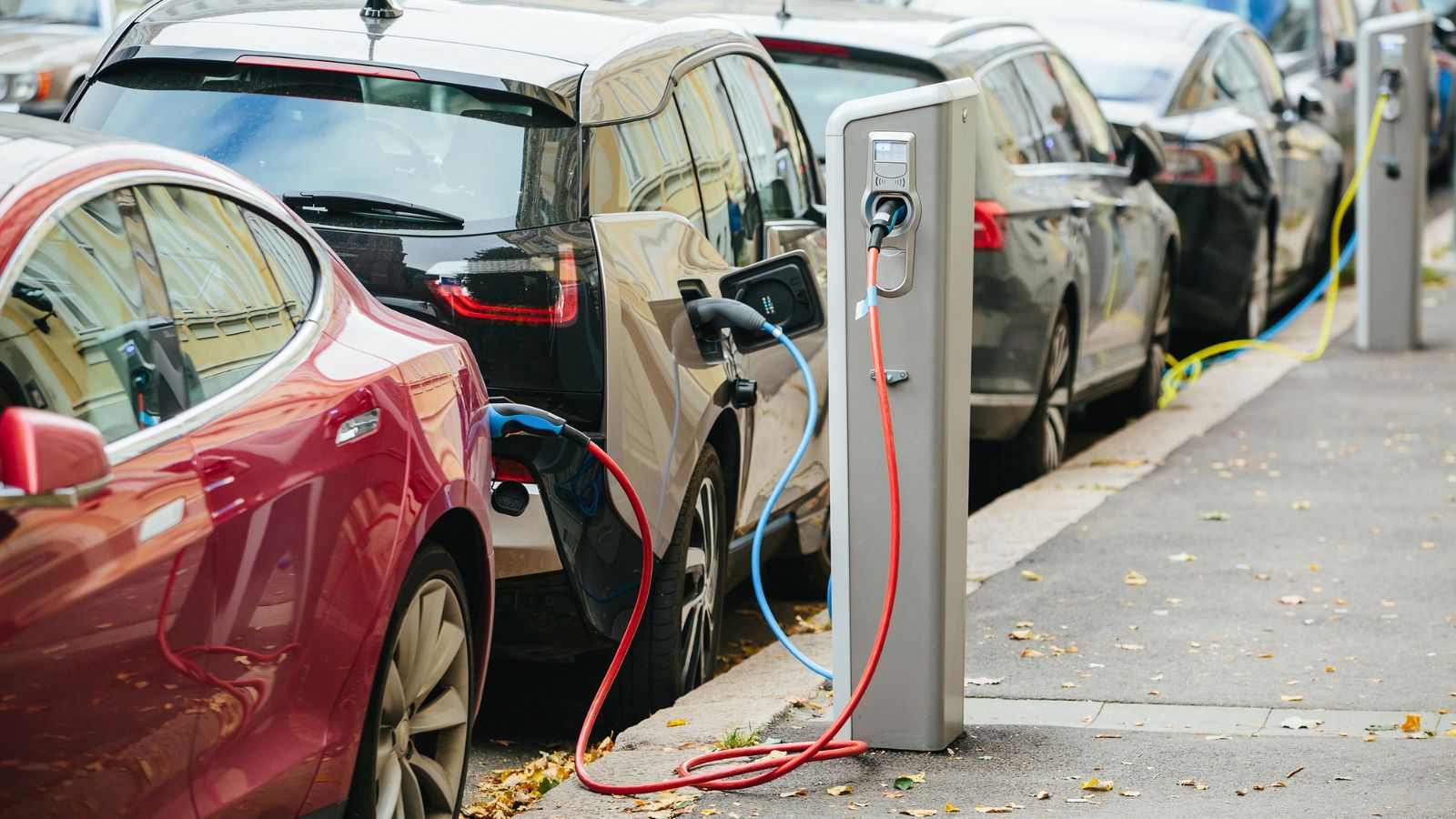
EVs were supposed to be Canada’s cash cow, but tariffs make them lame ducks. Battery components are now subject to cross-border tariffs, adding 9–14% to the cost of EV production. This increase is hindering production lines and delaying rollout schedules. Ingersoll and Windsor plants set to produce mass electric vehicles have lowered their estimates by 30%. Additionally, U.S. consumers are hesitant to pay the premium price, resulting in reduced order levels. If this trend continues, Canada’s ambition to produce 1.5 million electric vehicles (EVs) by 2030 could fall short by 400,000 units. Canada has one of the world’s largest lithium deposits, yet electric vehicle (EV) makers import battery cells from Asia.
Trucking Turmoil: Coast-to-Coast Logistics Disruptions
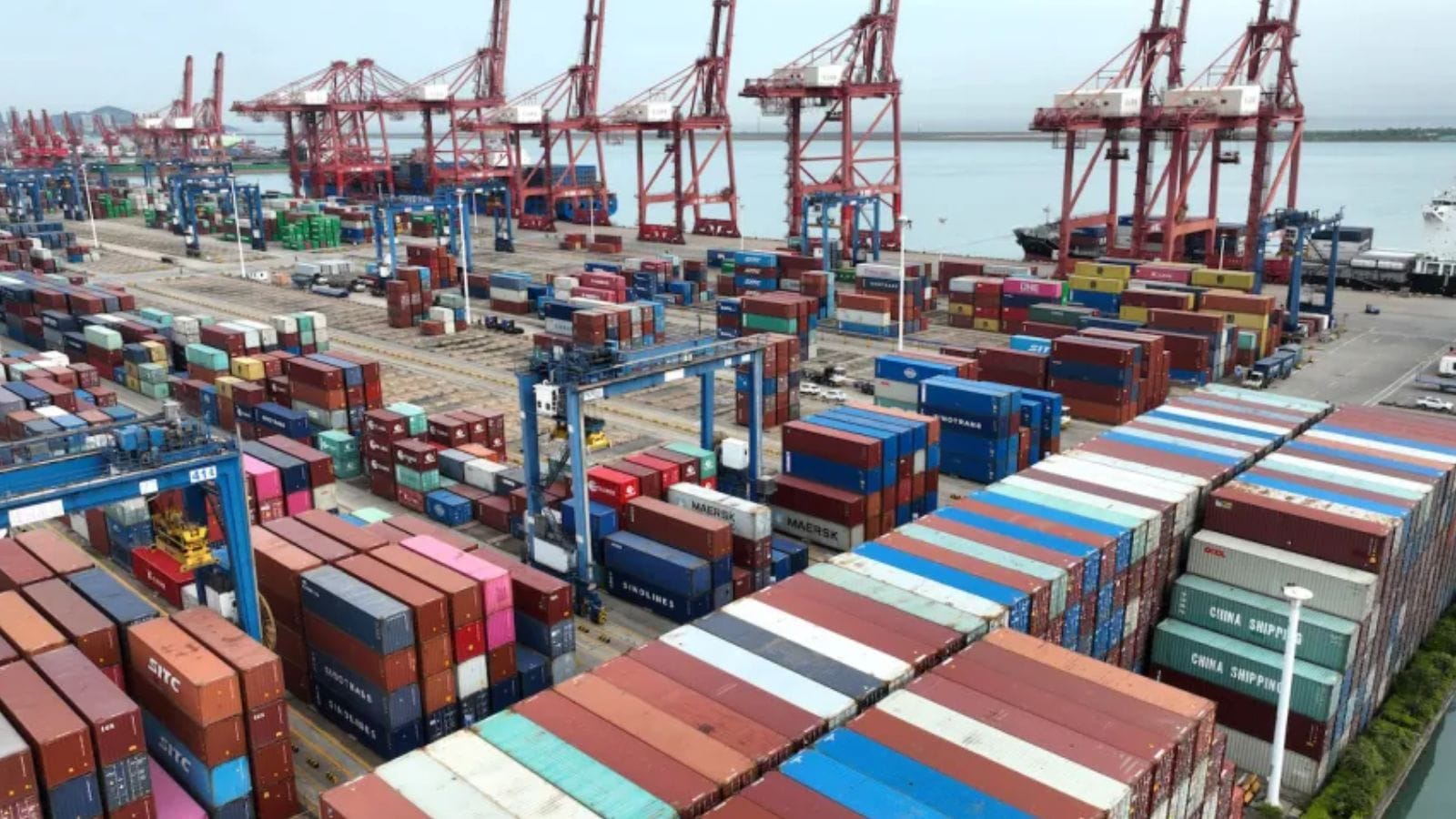
Trucking is the backroom motor of Canada’s auto sector, but it is also stuttering. Tariffs have added additional layers of inspection, increasing border crossing times by 22% on average. Delayed shipments have increased shipping costs by 15%. Carriers now charge “tariff premiums” to transport between Canadian and American auto centers. Driver shortages are also exacerbated, with trucking job vacancy rates rising by 11%. Some companies report they were forced to cut or consolidate their fleet, resulting in missed delivery times, delayed deliveries, and jammed assembly lines.
Border Bottlenecks: Delays That Cost Jobs
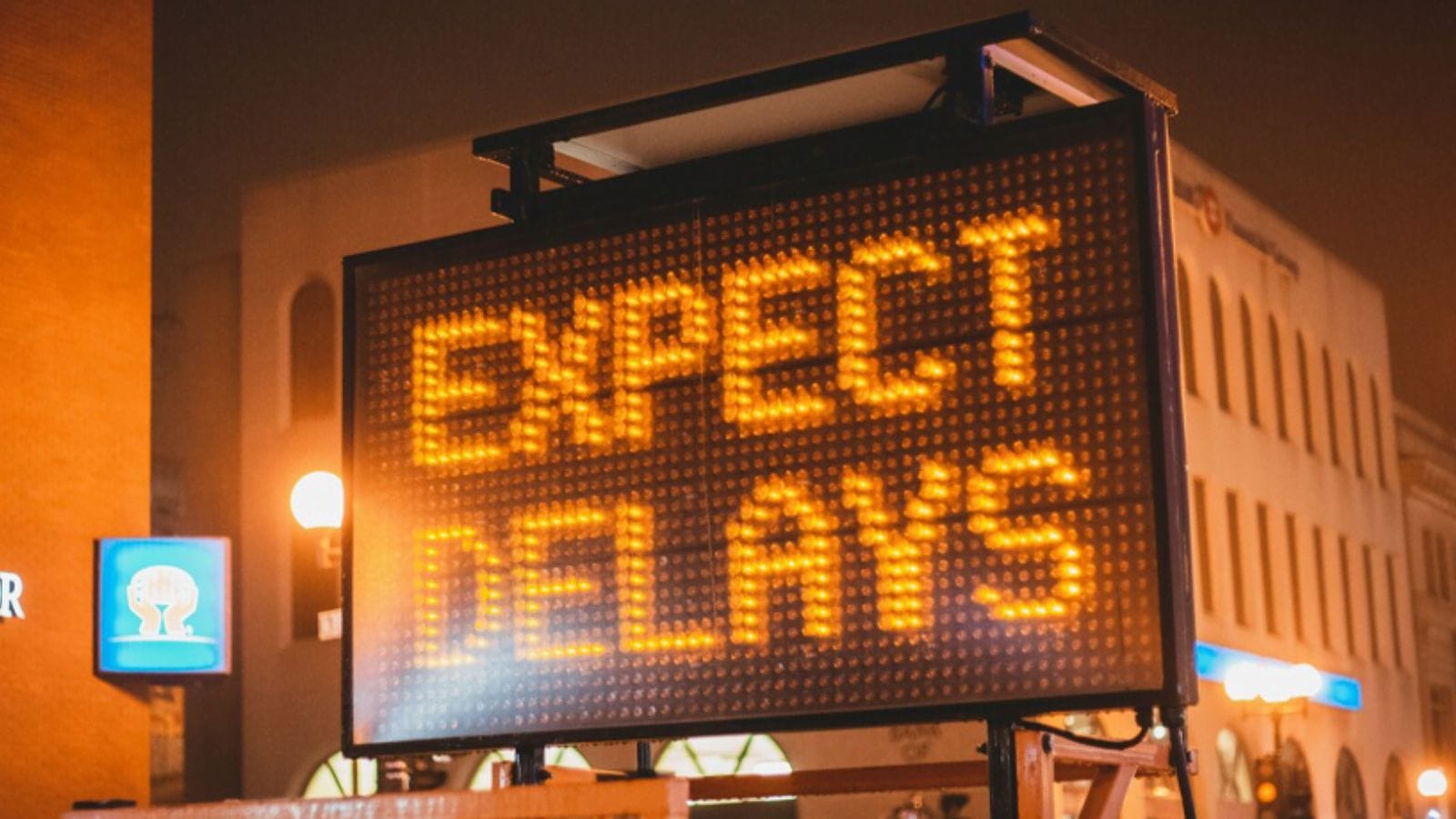
With increased post-tariff customs enforcement, Canada-U.S. border bottlenecks are a way of life. Average wait times for commercial crossings have increased by 45%, resulting in over $1.2 million per day in lost productivity for the industry. Truck plants running 24-hour part deliveries are experiencing compounded delays, leading to shift cancellations and occasional plant shutdowns. The Ambassador Bridge sees over 10,000 trucks cross it daily, and the entire area shuts down when it becomes clogged. Such bottlenecks erode job security and force companies to have skeleton shifts on standby, wasting money and morale. Over 7,000 jobs have been reduced by hours due to slowdowns at crossing points alone.
The Bigger Picture: What This Means for Canada’s Economy
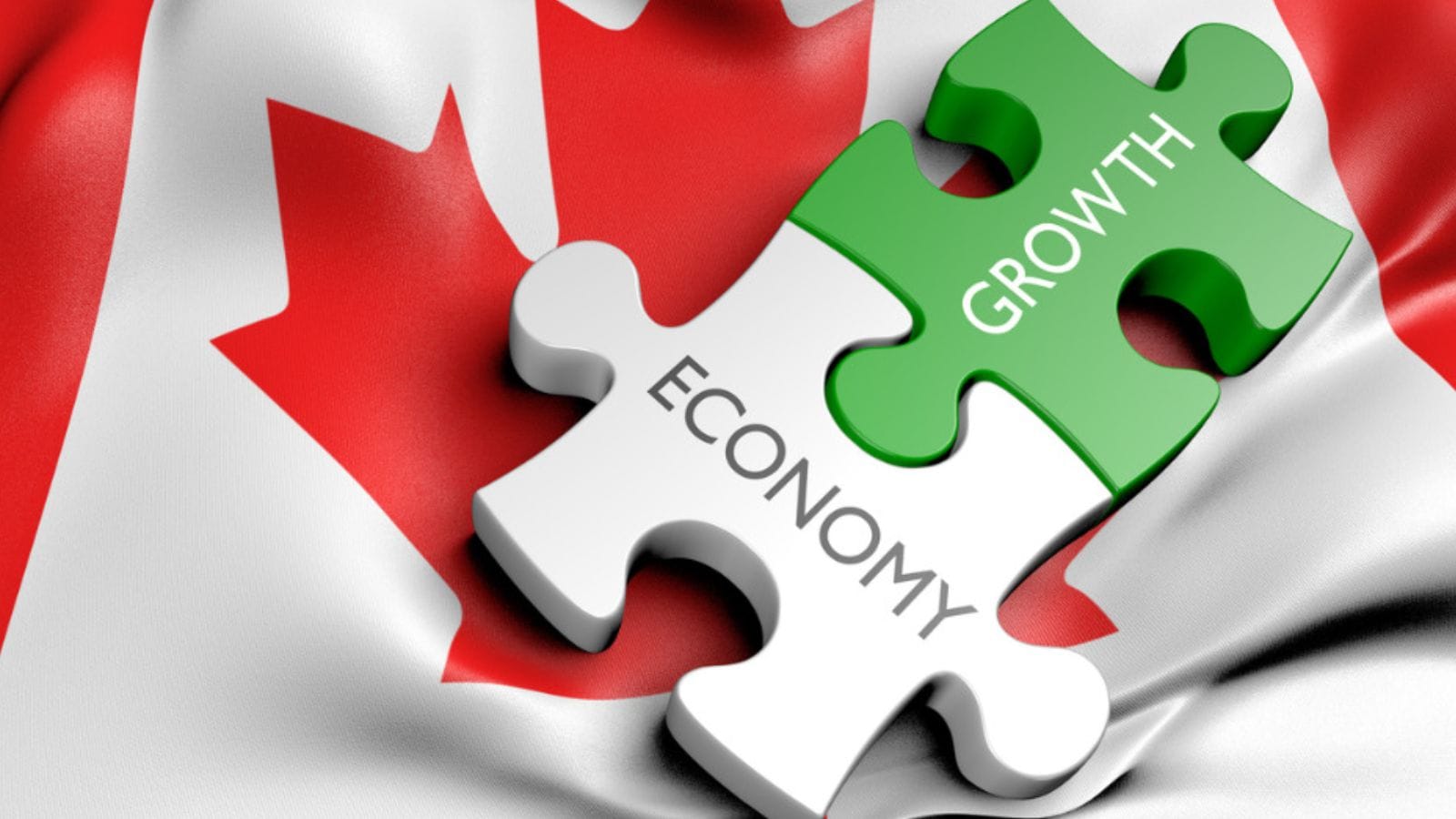
Taking a step back and looking at the bigger picture, the collective impact of tariffs on Canada’s automotive sector is substantial, causing significant pain to the national economy. The sector contributes over $19 billion annually to the GDP and supports more than 500,000 jobs. An estimated 12% decline would amount to a $2.3 billion loss of GDP and 55,000 job losses by the year’s close. Consumer sentiment is already worsening in car-dependent provinces. Revenue from provincial government taxes is also declining, which may reduce public expenditures on health, education, and infrastructure.
18 Budget-Friendly Electric Cars That Last Longer Than Their Loans — Economical Electrics
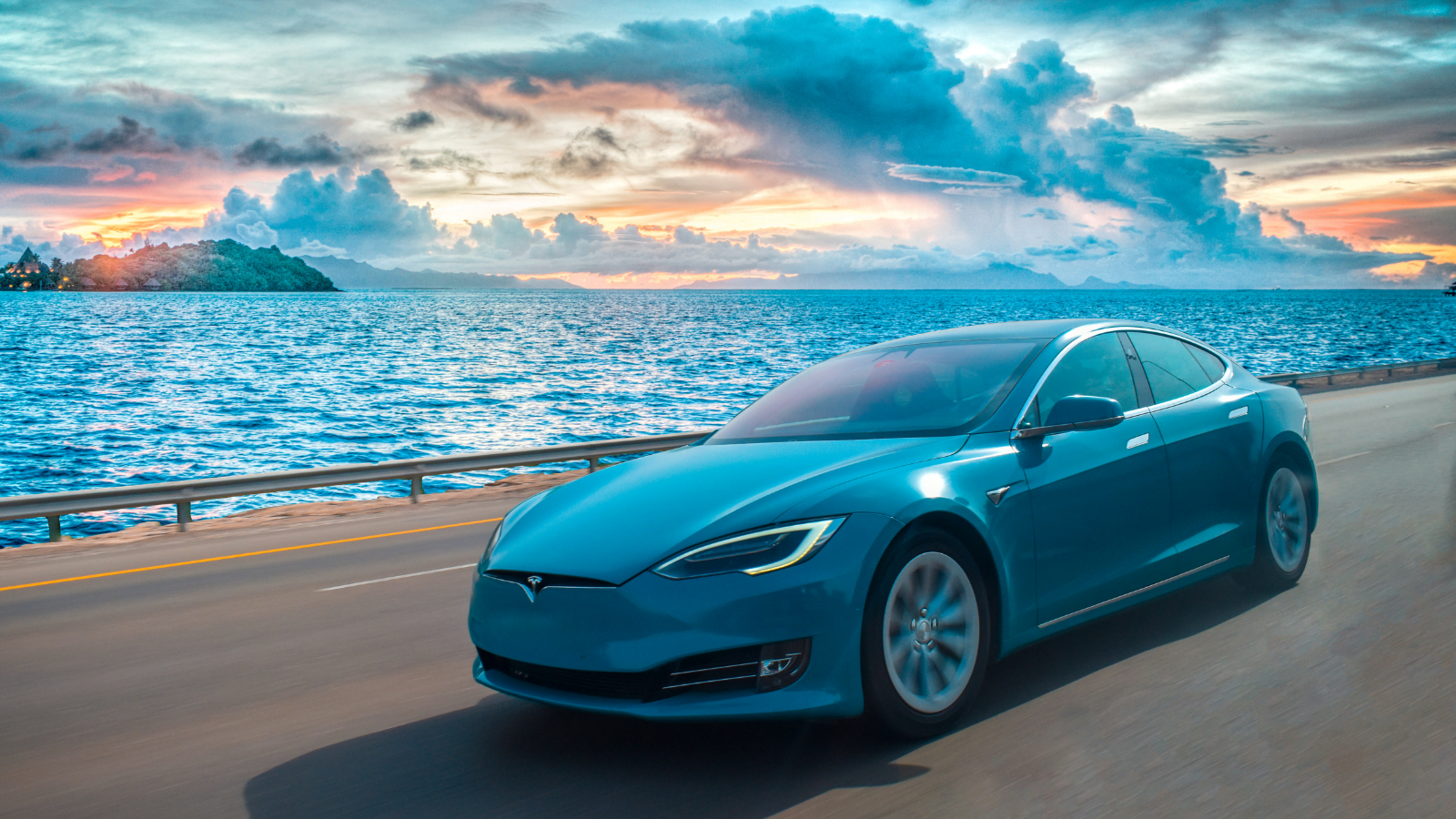
Electric vehicles are no longer a luxury for the elite—they’re a smart investment for the everyday driver. With manufacturers stepping up to the plate, affordable EVs now deliver on reliability, range, and modern comforts. Here’s a look at 18 economical electric cars engineered to outlast their payment plans.
18 Budget-Friendly Electric Cars That Last Longer Than Their Loans — Economical Electrics
