Canada’s auto parts industry has long been a quiet powerhouse, supporting thousands of jobs and supplying components to carmakers worldwide. But rising tariffs and trade uncertainty are now hitting these manufacturers hard. Even well-established companies are forced to adapt with cross-border supply chains disrupted and material costs climbing. These are 20 Canadian auto parts manufacturers facing challenges amid escalating tariff battles:
Magna International (Aurora, ON)
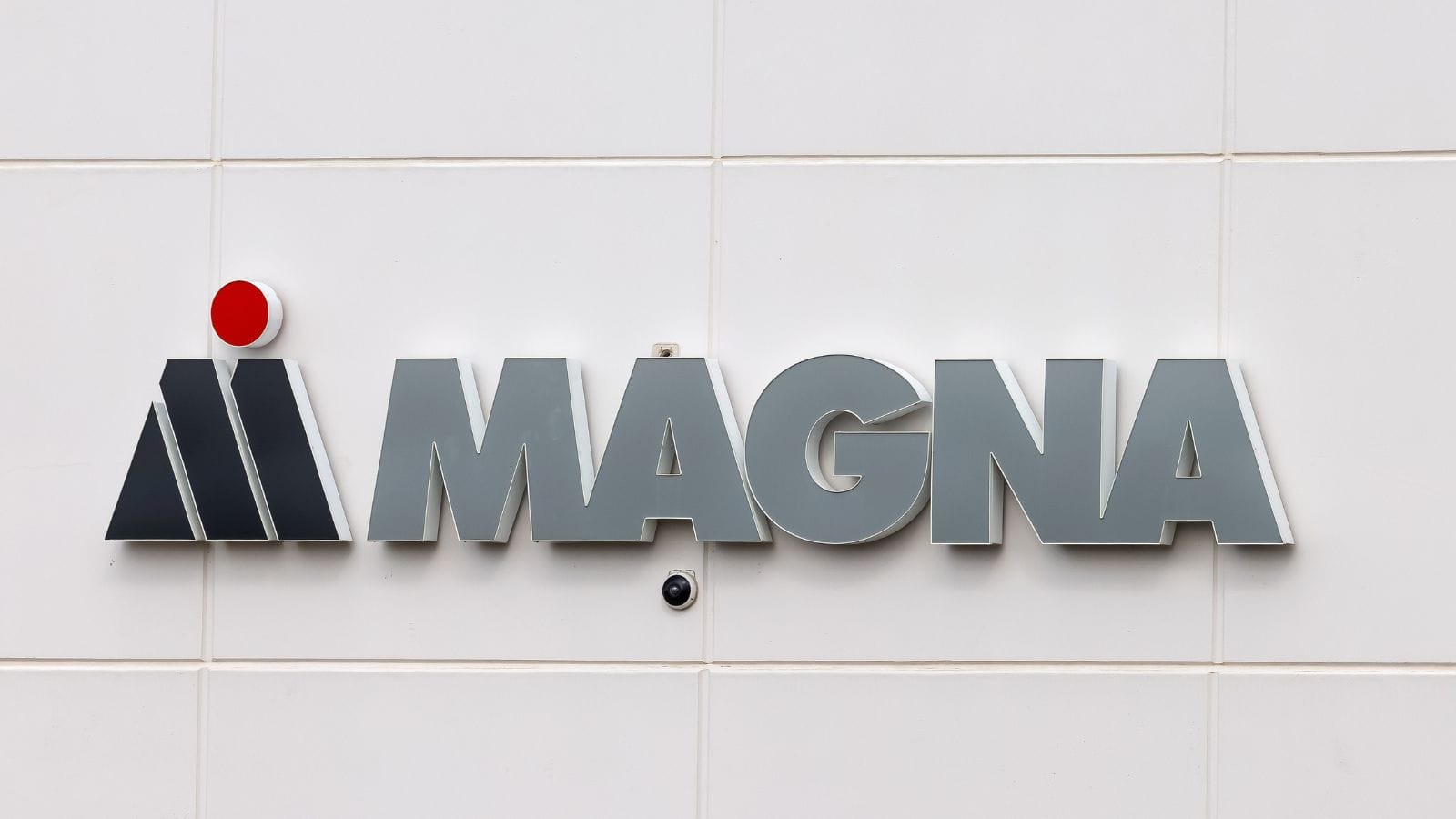
As Canada’s largest auto parts supplier, Magna is feeling the pressure from tariffs on both sides of the border. With operations in over 25 countries, the company’s global footprint is usually a strength, but reliance on cross-border trade has created cost and logistics challenges. Magna has warned investors of higher expenses tied to steel and aluminum duties and is exploring local sourcing. While still strong, the company must find ways to stay competitive without passing costs down to automakers.
Linamar Corporation (Guelph, ON)
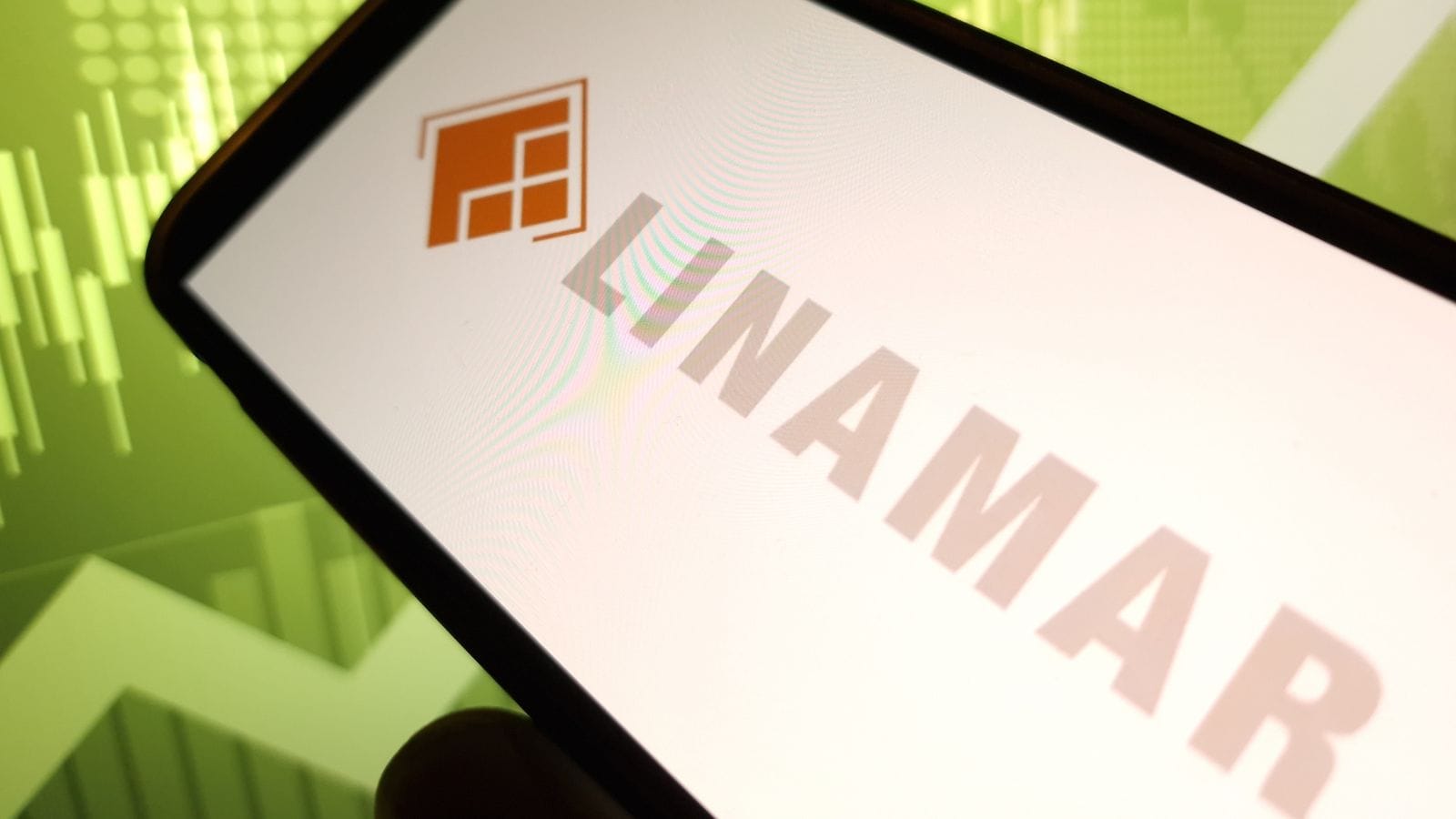
Linamar builds everything from powertrains to driveline systems and exports much of it to the U.S. Tariffs have increased the cost of materials like steel and aluminum, which are core to Linamar’s business. The company has responded by investing in automation and reducing reliance on imported parts. Executive leadership has voiced concerns about long-term uncertainty and rising production costs. Linamar remains a key supplier, but new tariffs force tough choices about future expansions and product line priorities.
Martinrea International (Vaughan, ON)
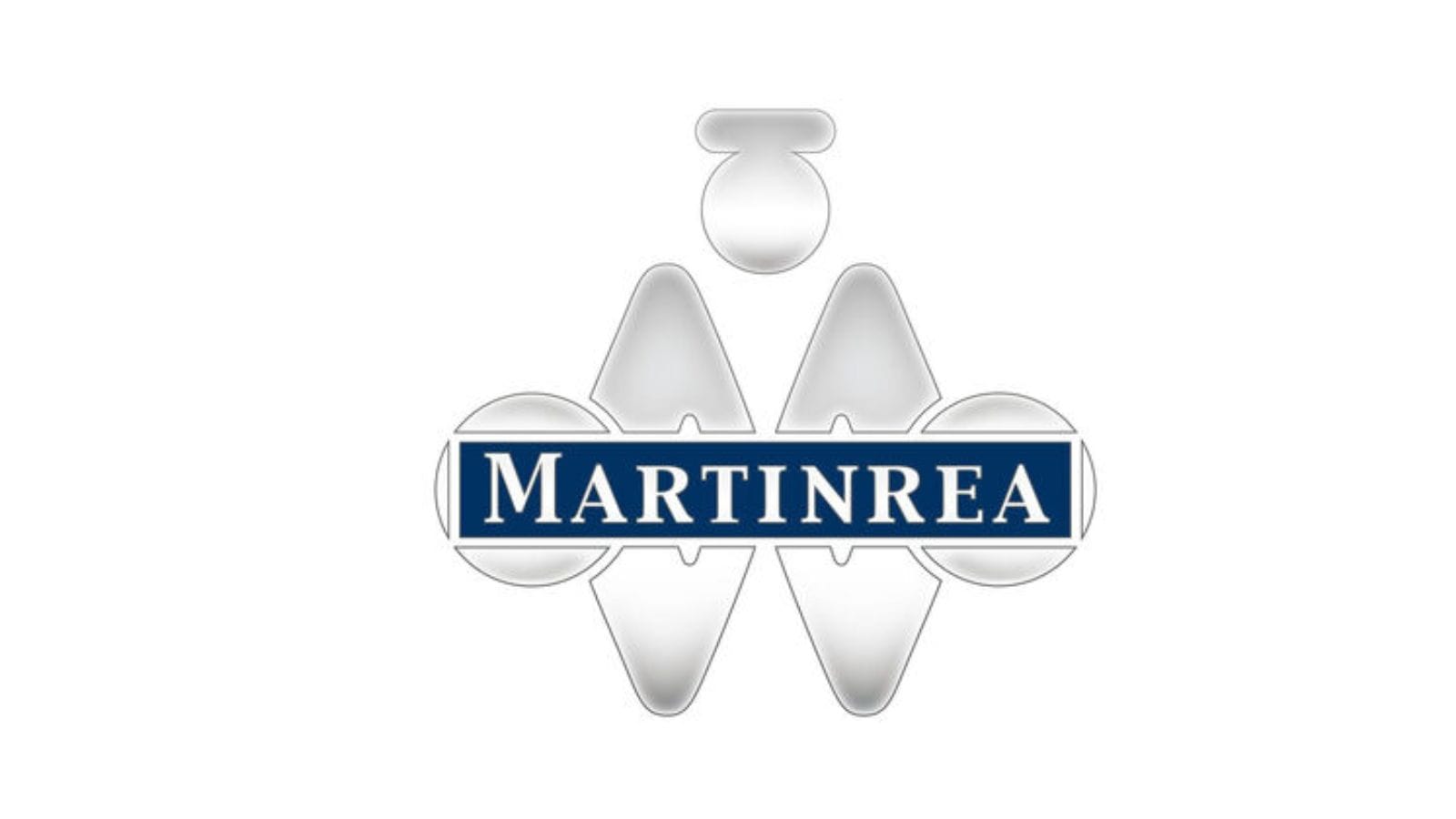
Martinrea specializes in lightweight structures, fluid systems, and complex assemblies. Tariff battles have disrupted its North American operations, with rising input costs squeezing already thin margins. The company continues to grow but has had to absorb significant price fluctuations in metals and plastics. Martinrea is increasing domestic sourcing and evaluating its international footprint to stay agile. While still posting profits, the company advocates for clearer trade rules to help stabilize a volatile sector that is directly affecting its workforce.
ABC Technologies (Toronto, ON)
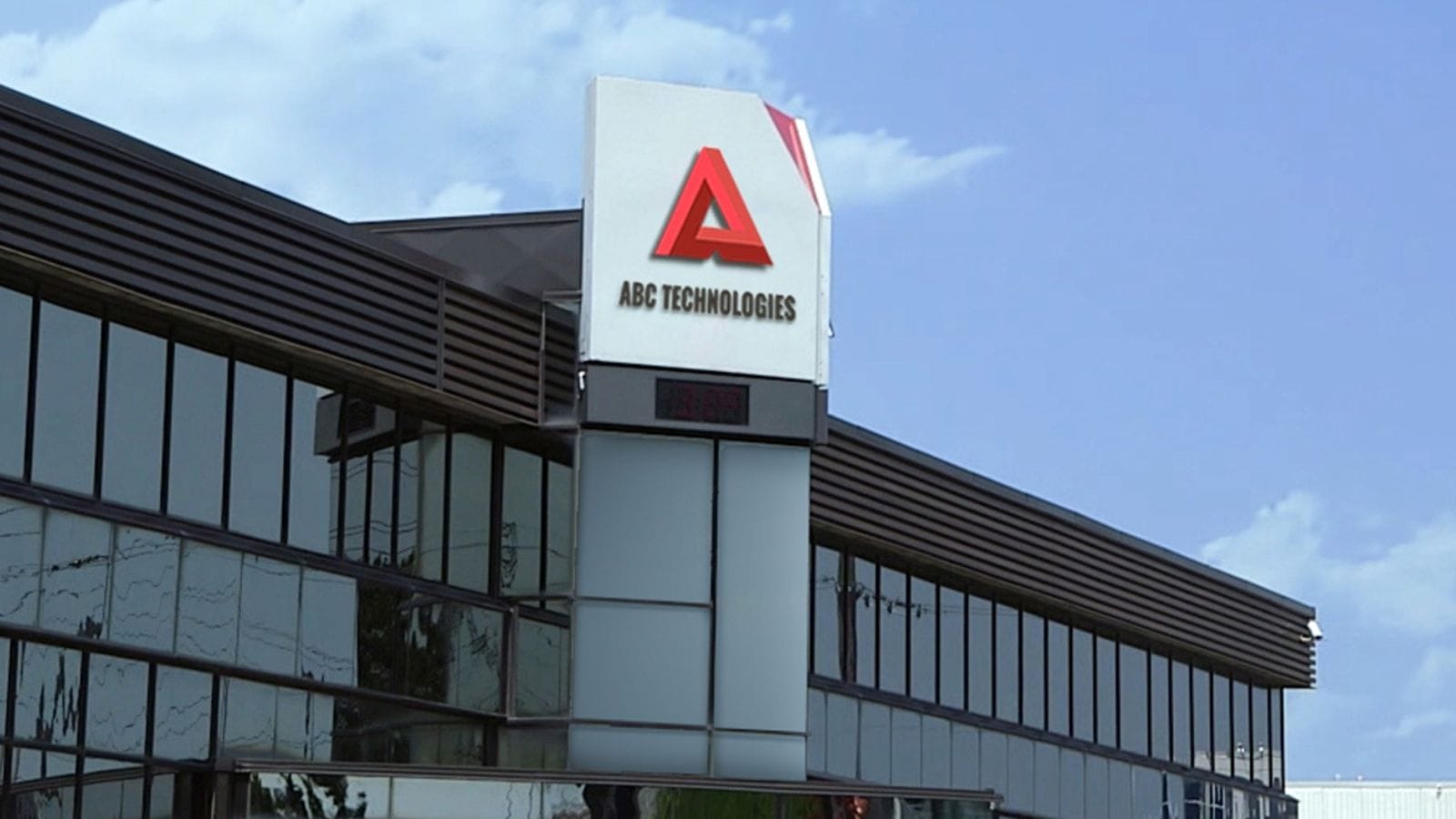
ABC Technologies supplies interior and exterior systems to several major automakers. With operations tied tightly to North American vehicle platforms, the company’s supply chain has taken a hit from ongoing tariffs on imported components. Lead times have increased, and material prices are cutting into profitability. ABC is working more closely with automakers on cost-sharing and sourcing alternatives to cope with it. However, the shifting trade landscape means long-term contracts are harder to predict, making financial planning more complex than ever before.
Multimatic Inc. (Markham, ON)
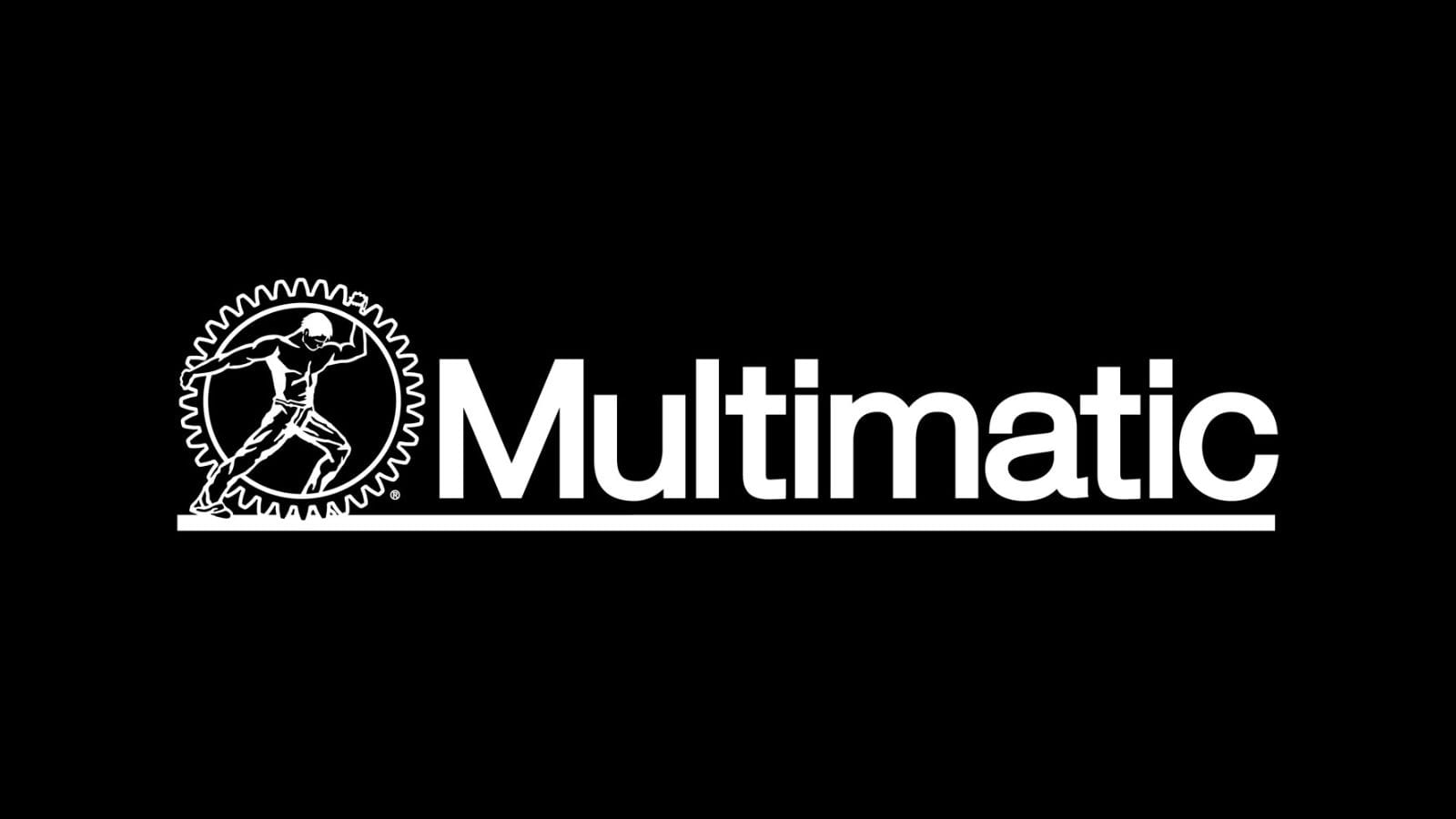
Known for its high-performance engineering and parts manufacturing, Multimatic builds components for everything from supercars to mainstream EVs. Tariffs on advanced materials and specialized parts have hit the company’s margins, particularly on limited-production runs. Despite these pressures, Multimatic continues to invest in R&D and has earned praise for its adaptive engineering. Still, supply chain uncertainty has complicated its global logistics strategy, and customers are increasingly sensitive to cost hikes, putting extra pressure on the company’s ability to innovate and deliver.
Stackpole International (Mississauga, ON)
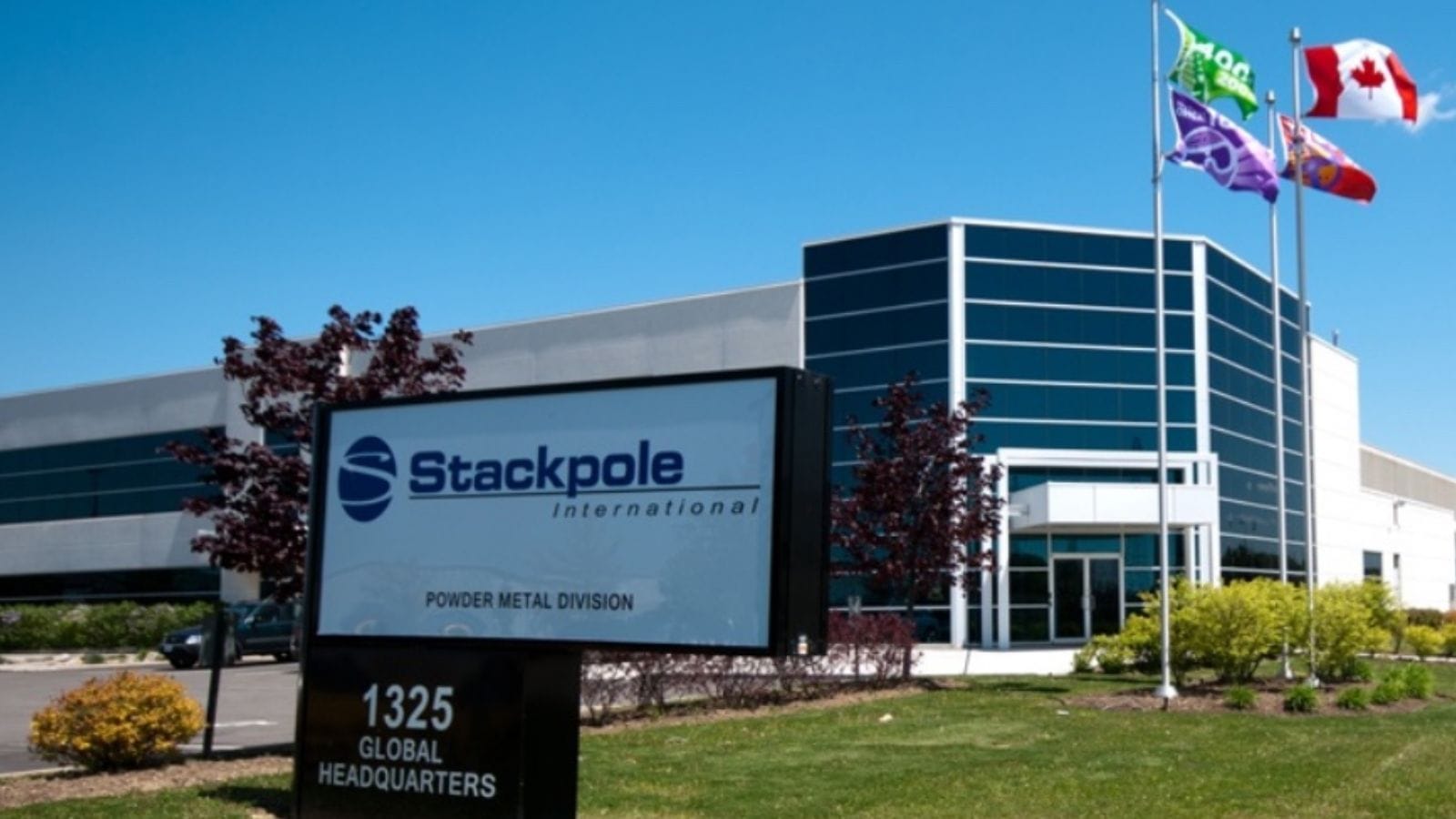
Stackpole manufactures pumps and powder metal components used in transmissions and powertrains. Its operations span North America, but many of its raw materials and machinery originate abroad. As tariffs increase on imported metals and industrial goods, Stackpole has been forced to review its procurement strategy. Production costs have risen, and the company is pressured to maintain delivery timelines for automakers.
Woodbridge Group (Mississauga, ON)
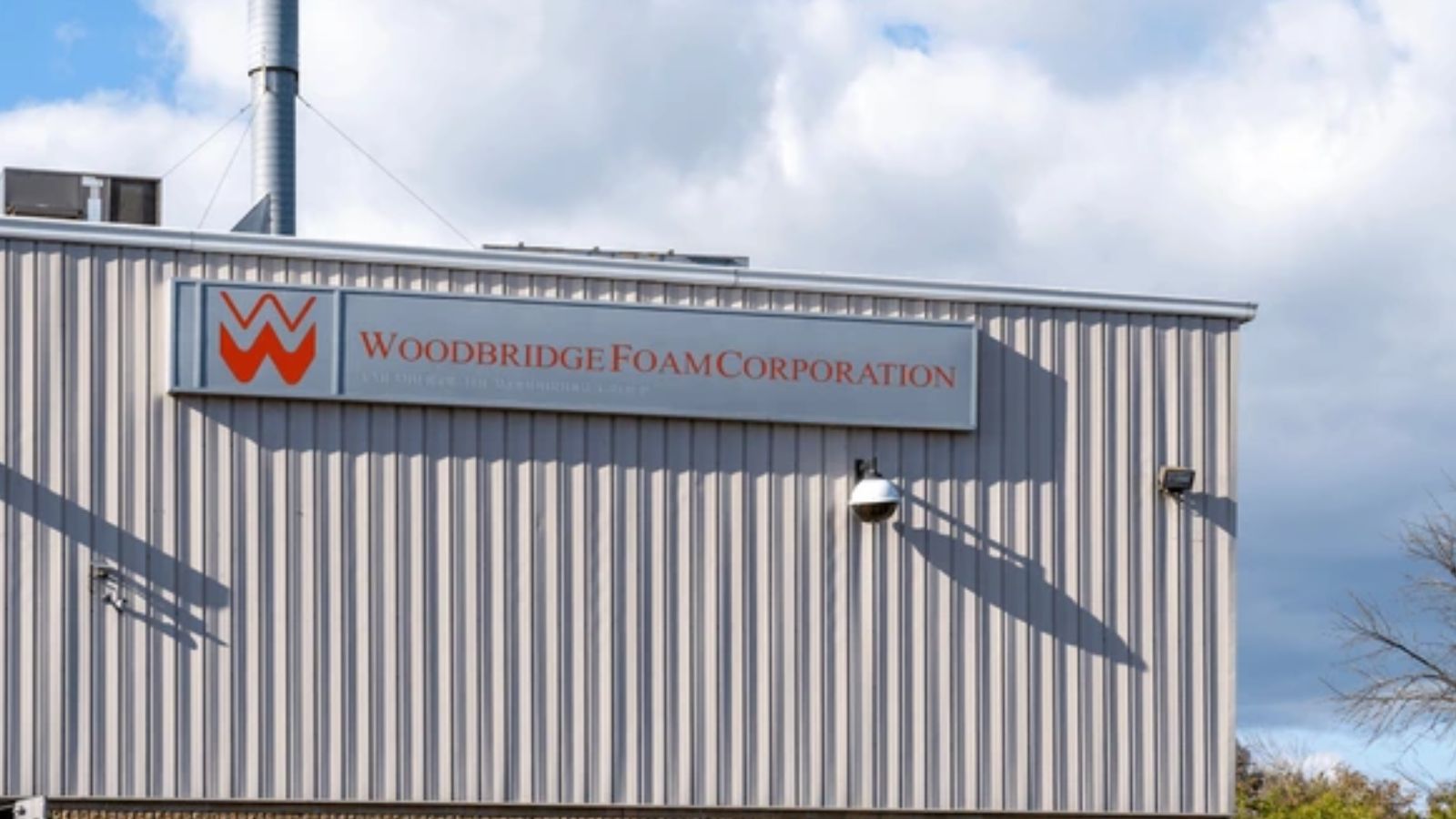
Specializing in polyurethane foam for car interiors, Woodbridge operates in a niche but essential space. The company’s global supply chain relies on specific chemicals and components that are now subject to fluctuating tariff rates. Woodbridge has had to reassess contracts and shift some manufacturing closer to North American sources as input prices climb. These adjustments haven’t been without cost.
Exco Technologies (Markham, ON)
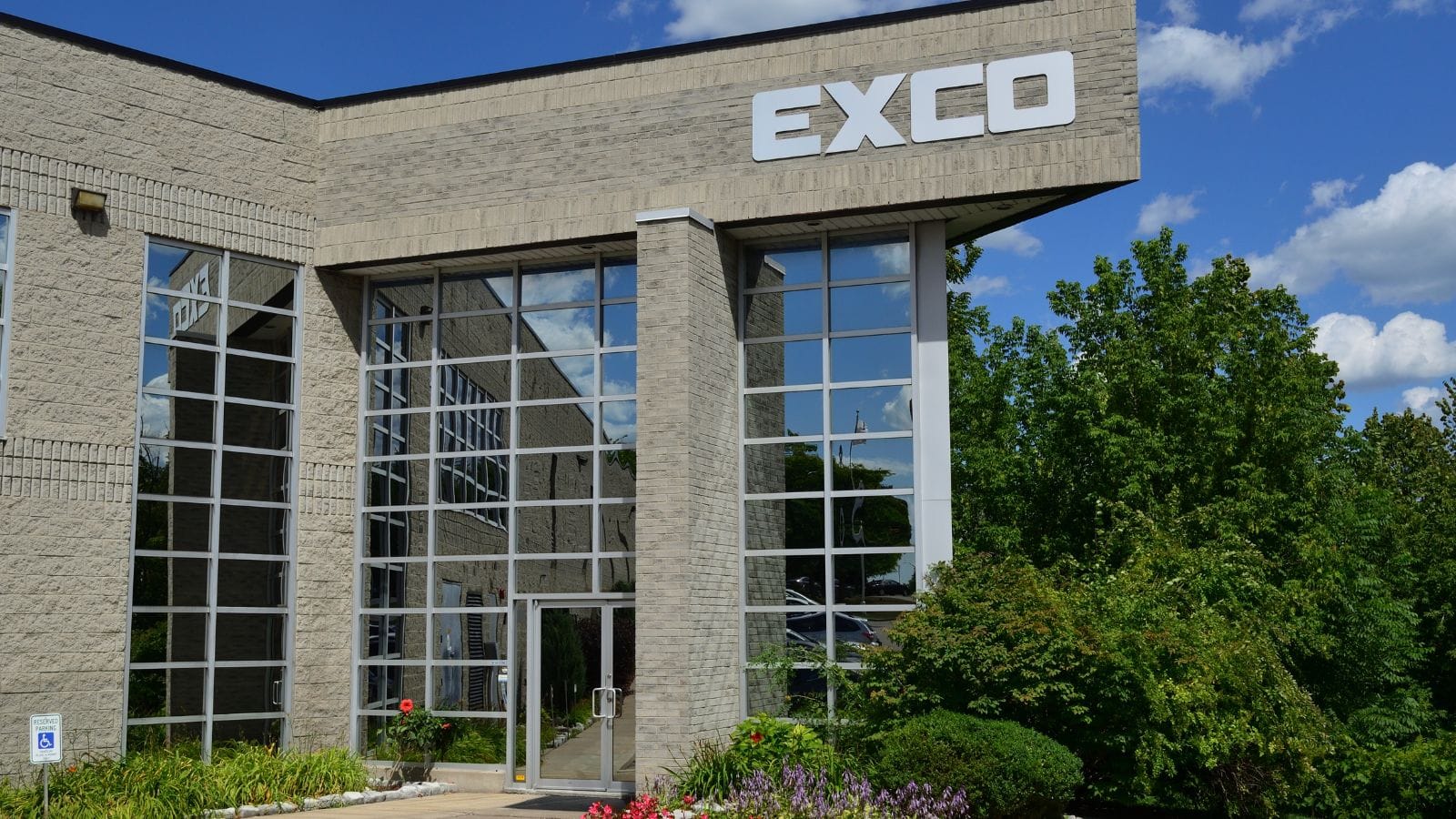
Exco builds tools, dies, and molds used in manufacturing car parts. The firm exports a large share of its equipment to U.S. plants, and any trade disruption has immediate consequences. Tariffs on metals and tooling parts have driven up prices, making it harder for Exco to stay competitive against foreign suppliers. In response, the company focuses more on local contracts and explores ways to reduce energy and production costs. While its global business remains strong, Exco is now more cautious about expanding into uncertain trade regions.
Wescast Industries (Brantford, ON)
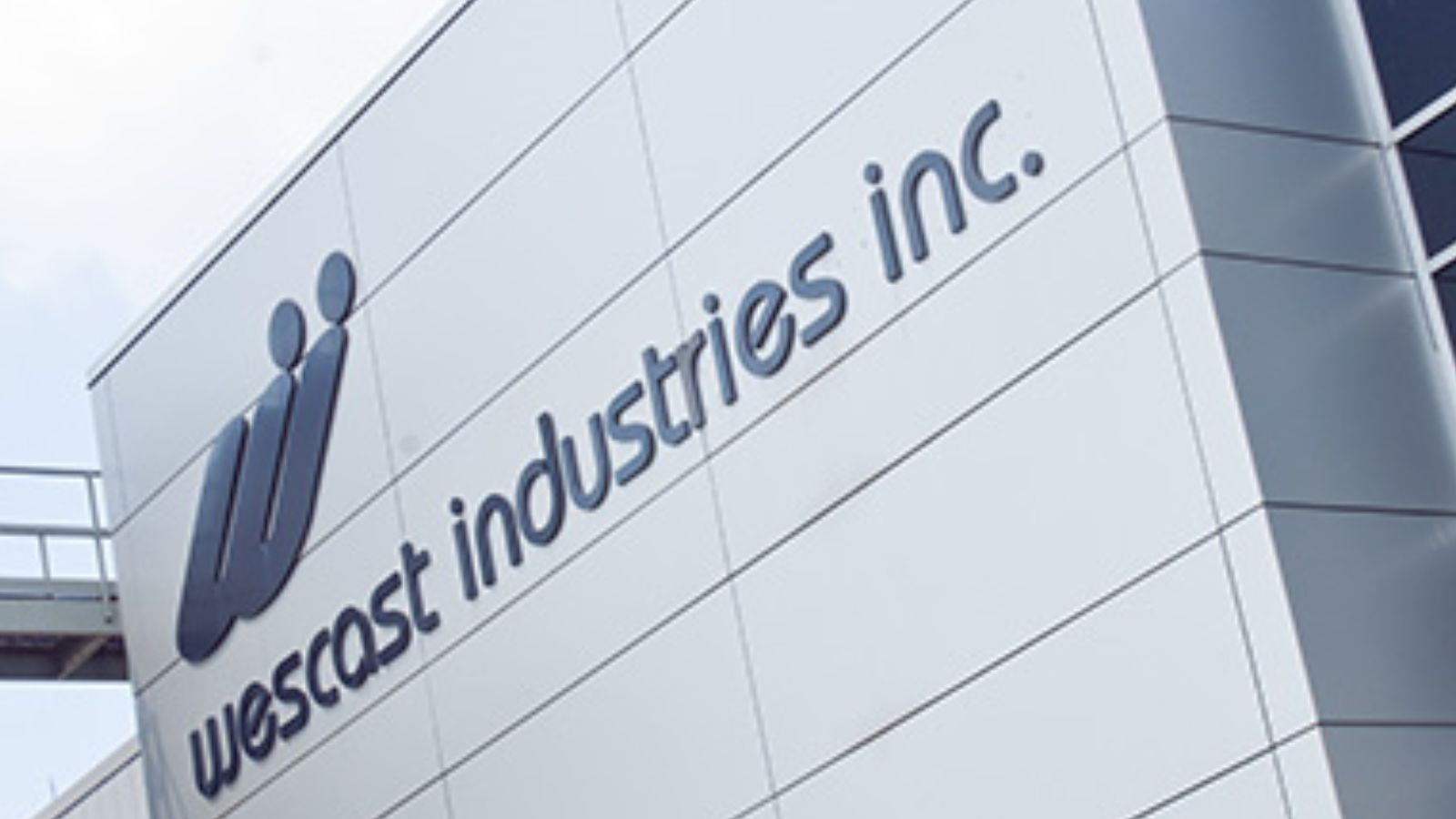
Wescast, a major supplier of exhaust manifolds and turbocharger housings, has been facing pricing pressure due to tariffs on specialty metals. The company sources some materials from Asia and Europe, which have become more expensive under new trade rules. Increased shipping costs and border delays have only added to the challenge. Wescast has maintained production but is working closely with its OEM partners to reevaluate long-term supply agreements. The company’s ability to remain competitive in this climate will likely depend on how quickly tariffs are resolved.
Spectra Premium (Boucherville, QC)
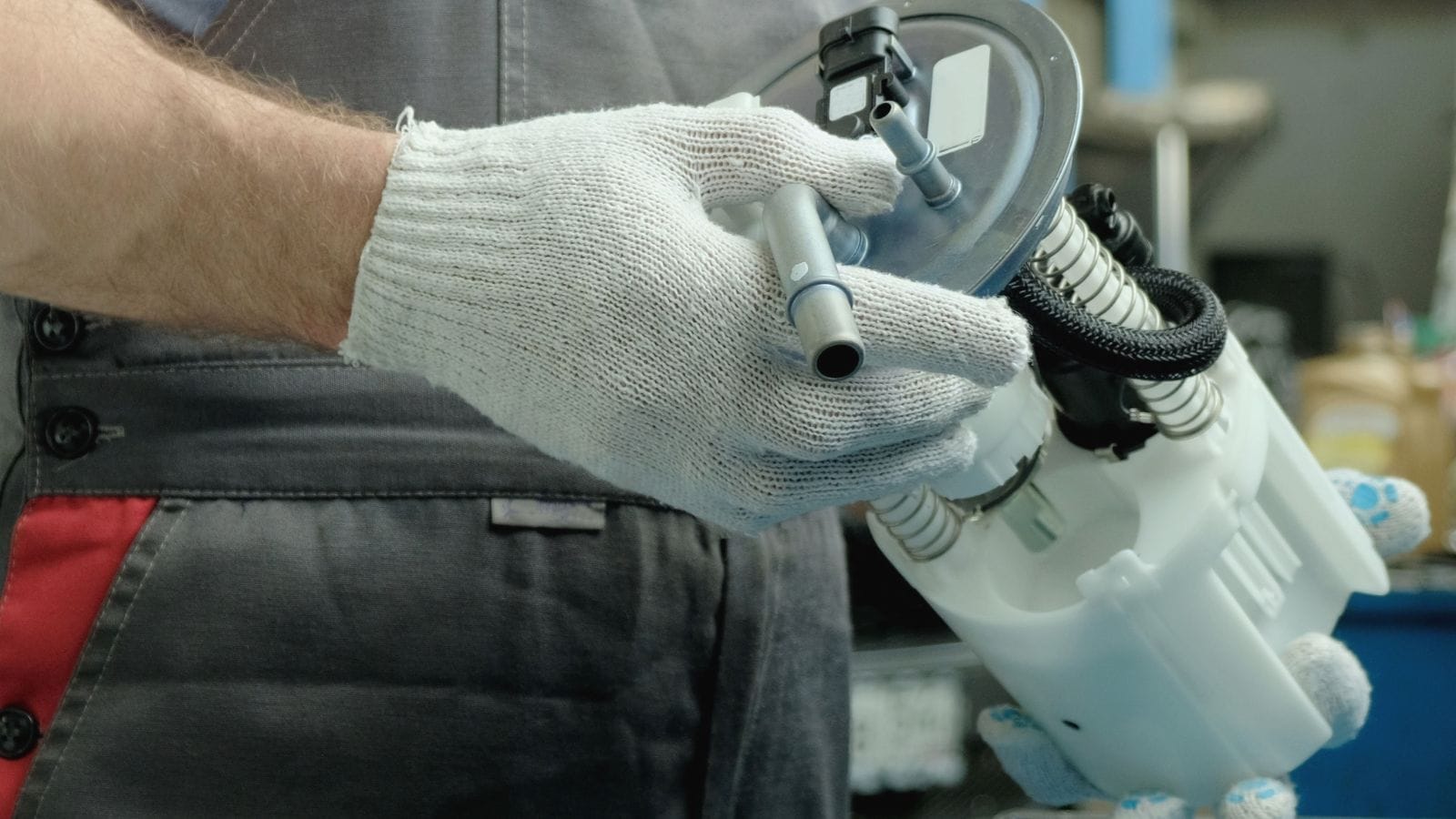
Spectra Premium is known for producing fuel system components, radiators, and engine oil pans. Many of these parts rely on imported materials and offshore manufacturing partners, making the company especially sensitive to new tariffs. Spectra has begun shifting some operations domestically to control costs and improve reliability, but this comes when inflation is already squeezing operations.
Axiom Group (Aurora, ON)

Axiom Group supplies precision plastic components from dashboards to under-hood parts. With some of its key materials and molds sourced globally, rising tariffs have made it harder to forecast costs. While the company has invested heavily in automation to stay competitive, unpredictable trade shifts have impacted long-term pricing and delivery schedules. Axiom is working more closely with clients to renegotiate timelines and supply agreements. Its future growth plans remain strong, but leadership admits the current environment requires constant adjustments to remain profitable and responsive to OEM expectations.
Plasman (Windsor, ON)
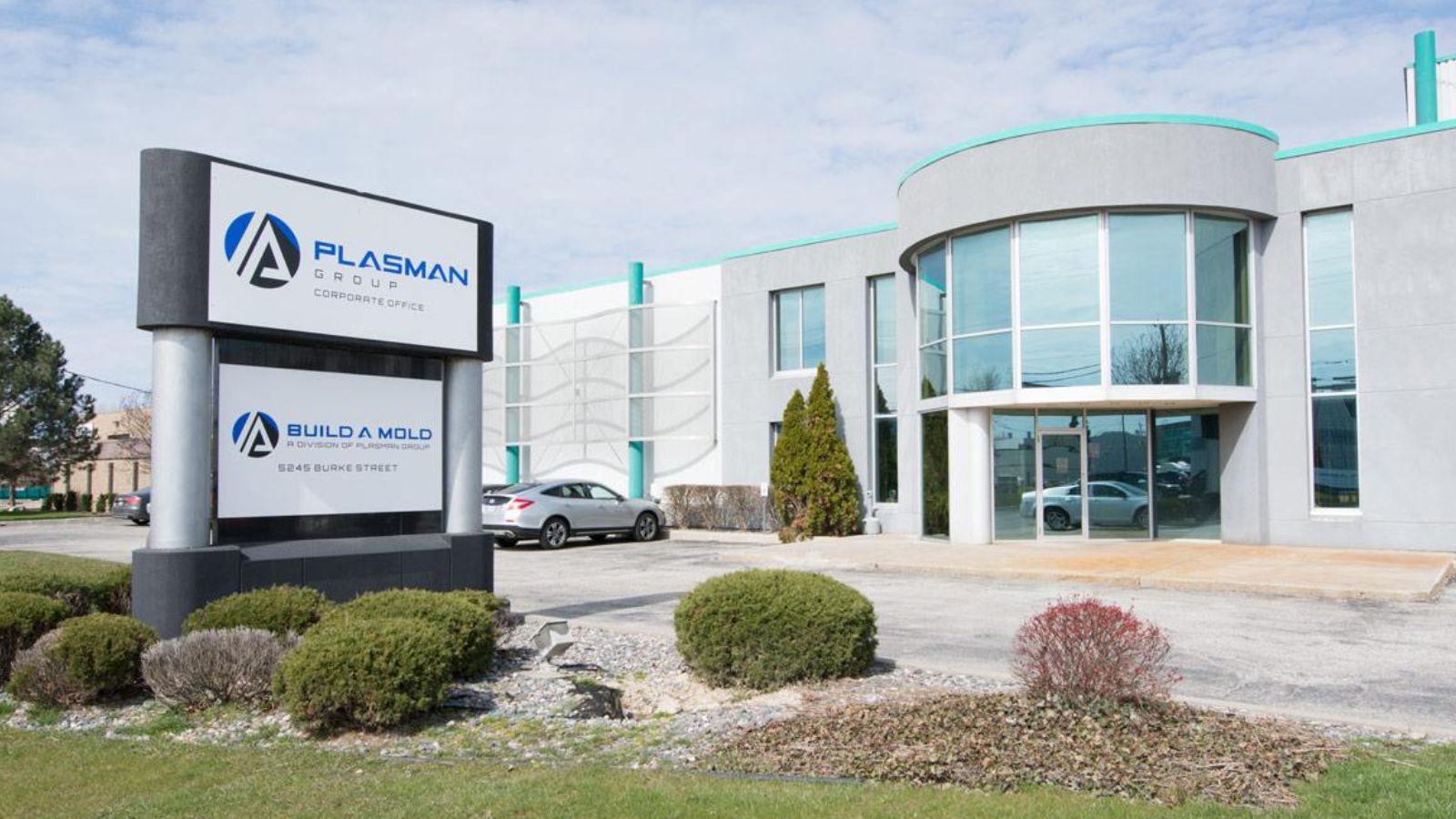
Plasman, formerly Plastal, produces plastic and metal automotive components, including bumpers and grilles. As tariffs disrupt trade routes, Plasman’s global reach has become more complex, with multiple locations across North America and Europe. The company faces longer lead times and higher costs, particularly when shipping parts between border facilities. Despite this, Plasman continues to invest in local production and employee training to offset external pressures.
D&V Electronics (Woodbridge, ON)
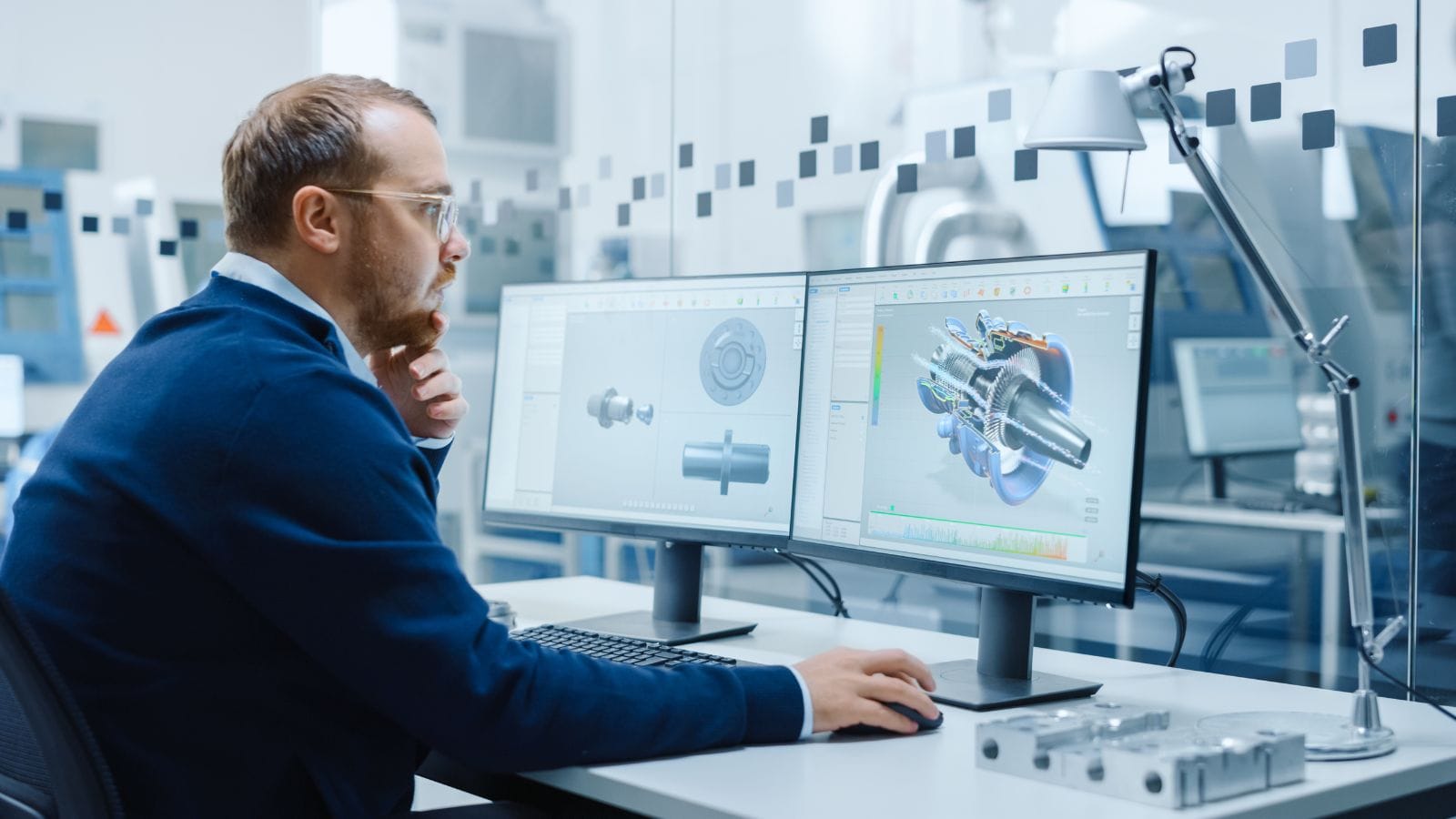
D&V Electronics builds testing equipment for electric motors, a fast-growing market alongside EV adoption. However, the components that power this testing technology often come from overseas and are now caught in tariff battles. This has driven up prices and delayed key deliveries, affecting D&V’s ability to meet contract deadlines. The company is exploring domestic alternatives and tighter inventory control to keep operations on track. While demand remains strong, D&V is dealing with real pressures that could slow its growth if supply chain instability continues.
Samco Machinery (Toronto, ON)
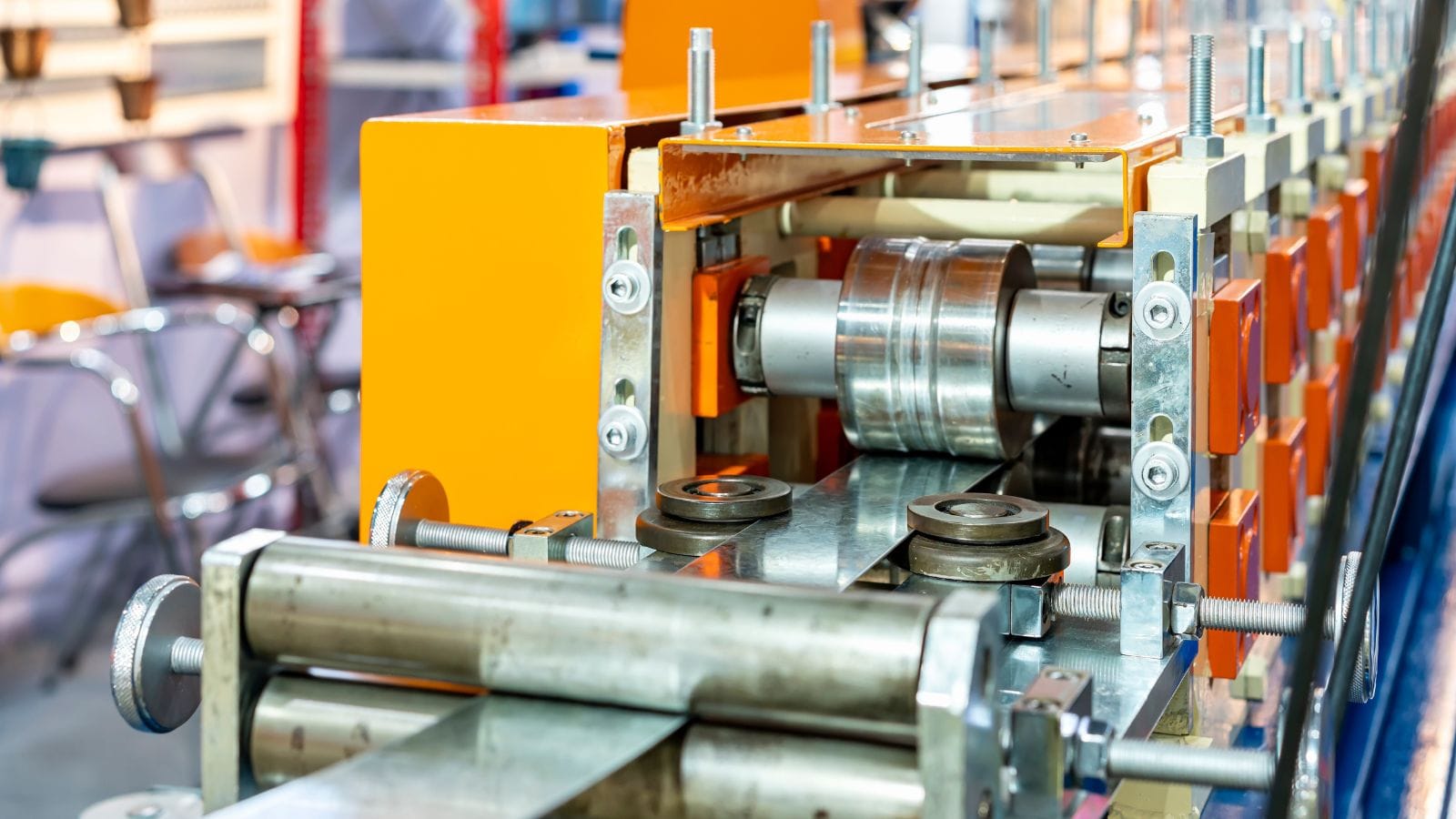
Samco builds custom roll-forming machines used in the auto and industrial sectors. Much of the precision equipment and metals used in production are imported, making Samco especially vulnerable to tariff hikes. These added costs are hitting Samco as it tries to expand its presence in the EV and lightweight vehicle markets. Samco has responded by increasing North American sourcing and lobbying for trade exemptions, but unpredictability remains a key concern. The firm maintains client price stability without cutting back on innovation or quality.
Techform Group (Penetanguishene, ON)
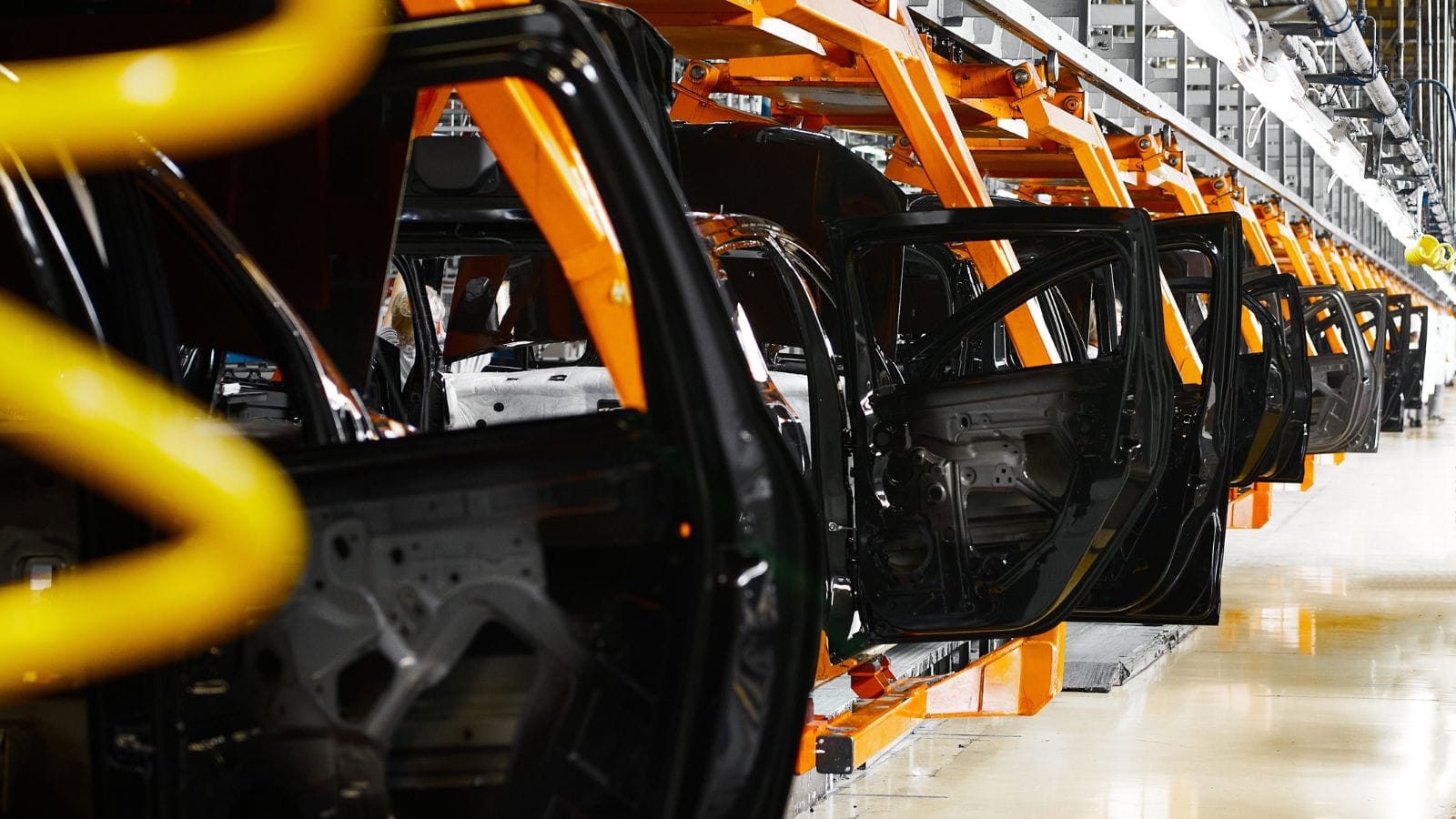
Techform is a leading supplier of hinge systems and complex car door and hatches mechanisms. Its components are often built using specialized alloys that have become harder to import under current trade tensions. Shipping and customs delays have disrupted production schedules, forcing the company to increase safety stock and seek new suppliers. These changes require both time and capital. Techform is known for high precision and reliability. Still, it’s now facing an uphill climb to protect its margins while preserving its reputation in a market where expectations haven’t lowered, even as costs rise.
Novipax (Vancouver, BC)
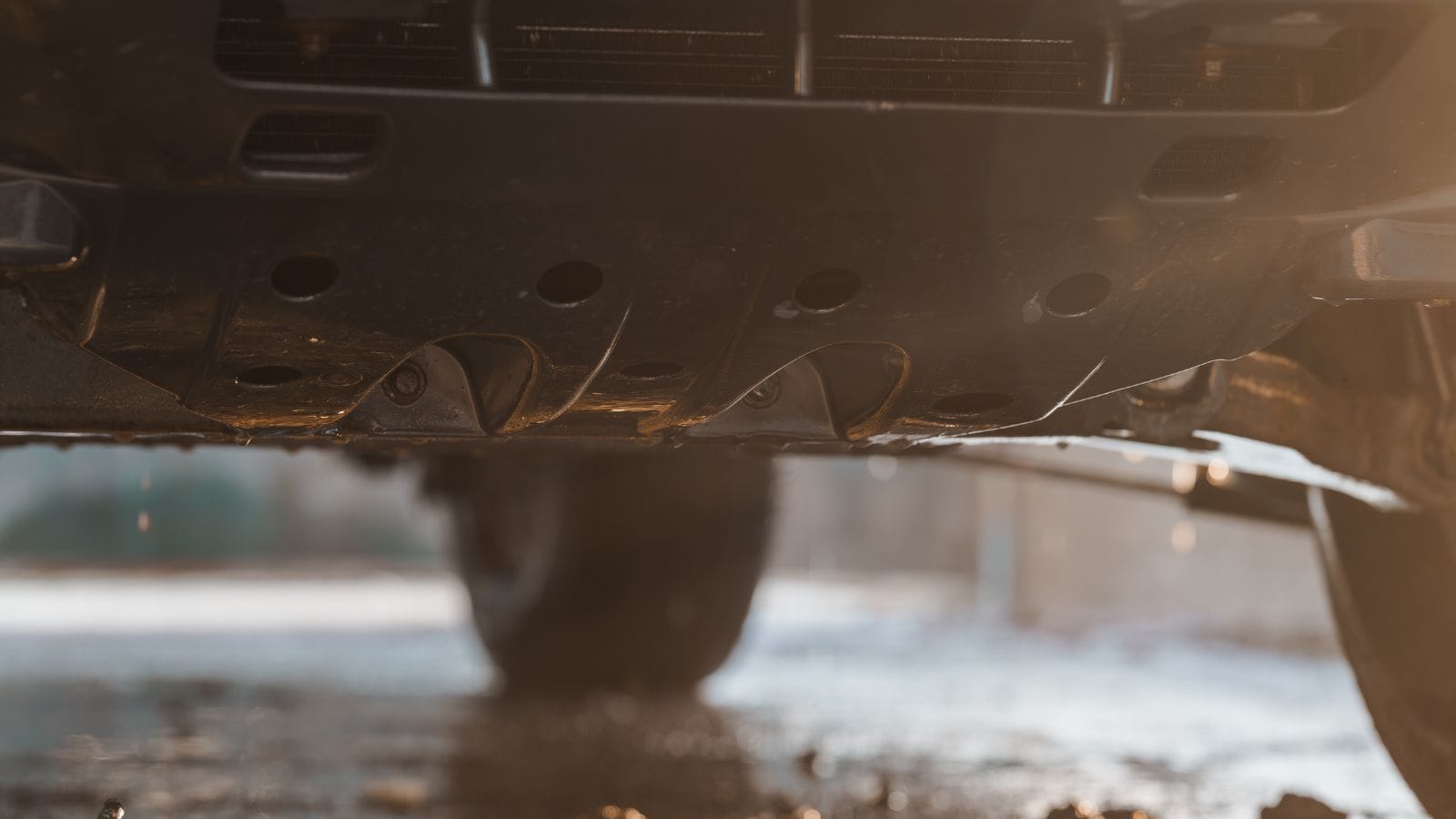
Novipax specializes in plastic components like fuel systems and underbody shields. Tariffs on raw materials and plastics have pushed costs higher, squeezing margins. The company is exploring alternative materials and regional suppliers but faces certification and quality control challenges. Shipping delays due to border inspections have also affected production schedules. Despite these hurdles, Novipax remains committed to innovation and meeting automaker demands. However, ongoing tariff battles have increased uncertainty, forcing the company to focus more on flexible manufacturing strategies and inventory management to stay competitive in a challenging market.
Ennis-Flint, Canada (Mississauga, ON)
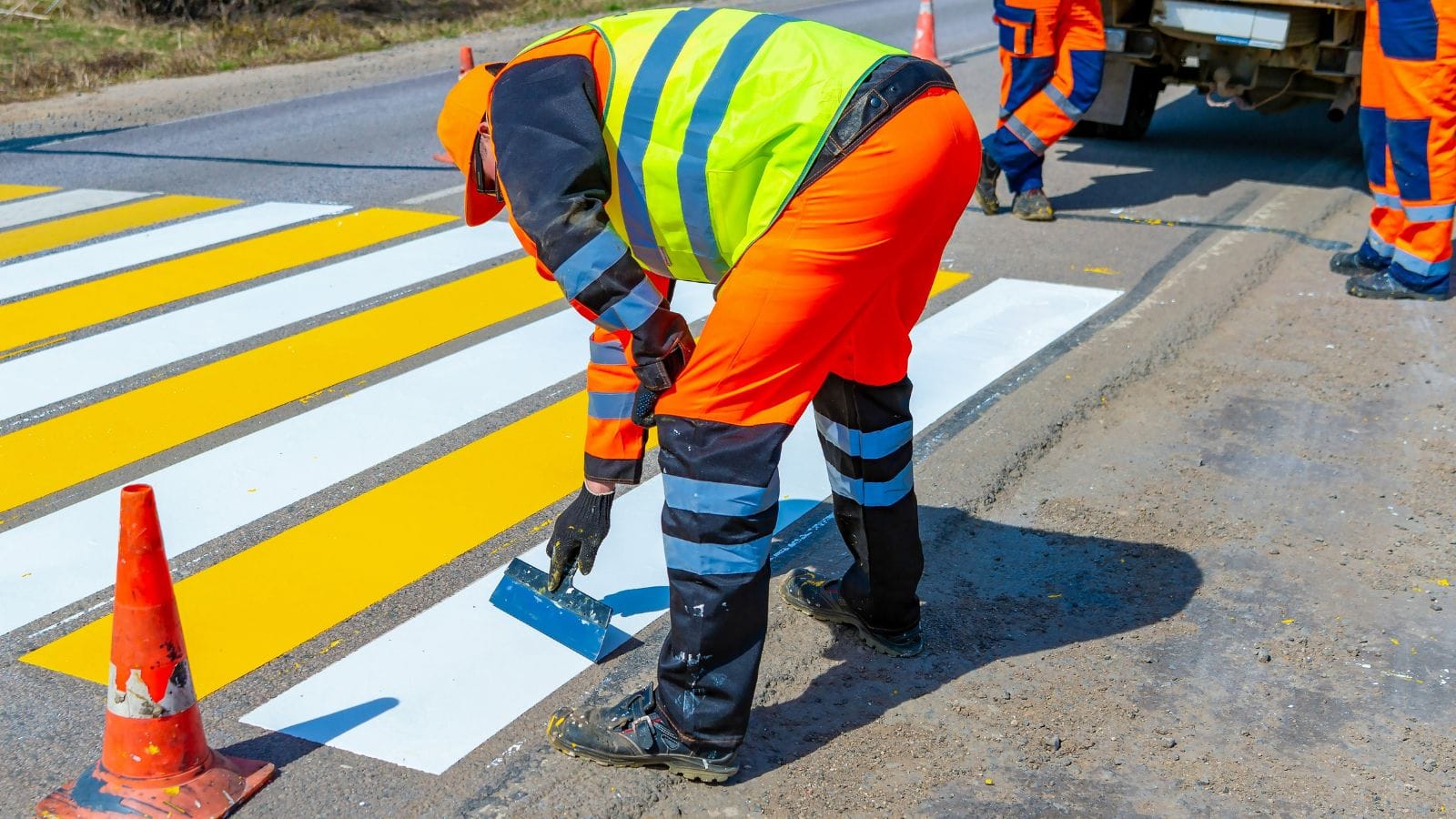
Ennis-Flint Canada provides road safety products used around automotive manufacturing facilities and testing grounds. Tariffs on metal components and coatings have increased the cost of production and distribution. Though not a direct auto parts maker, its role in the supply chain makes it vulnerable to trade issues. The company has increased local sourcing and adjusted pricing strategies to maintain contracts. Rising tariffs have made planning difficult, but Ennis-Flint is investing in supply chain resilience to protect jobs and keep safety products flowing without interruption.
Cambro Manufacturing (Toronto, ON)
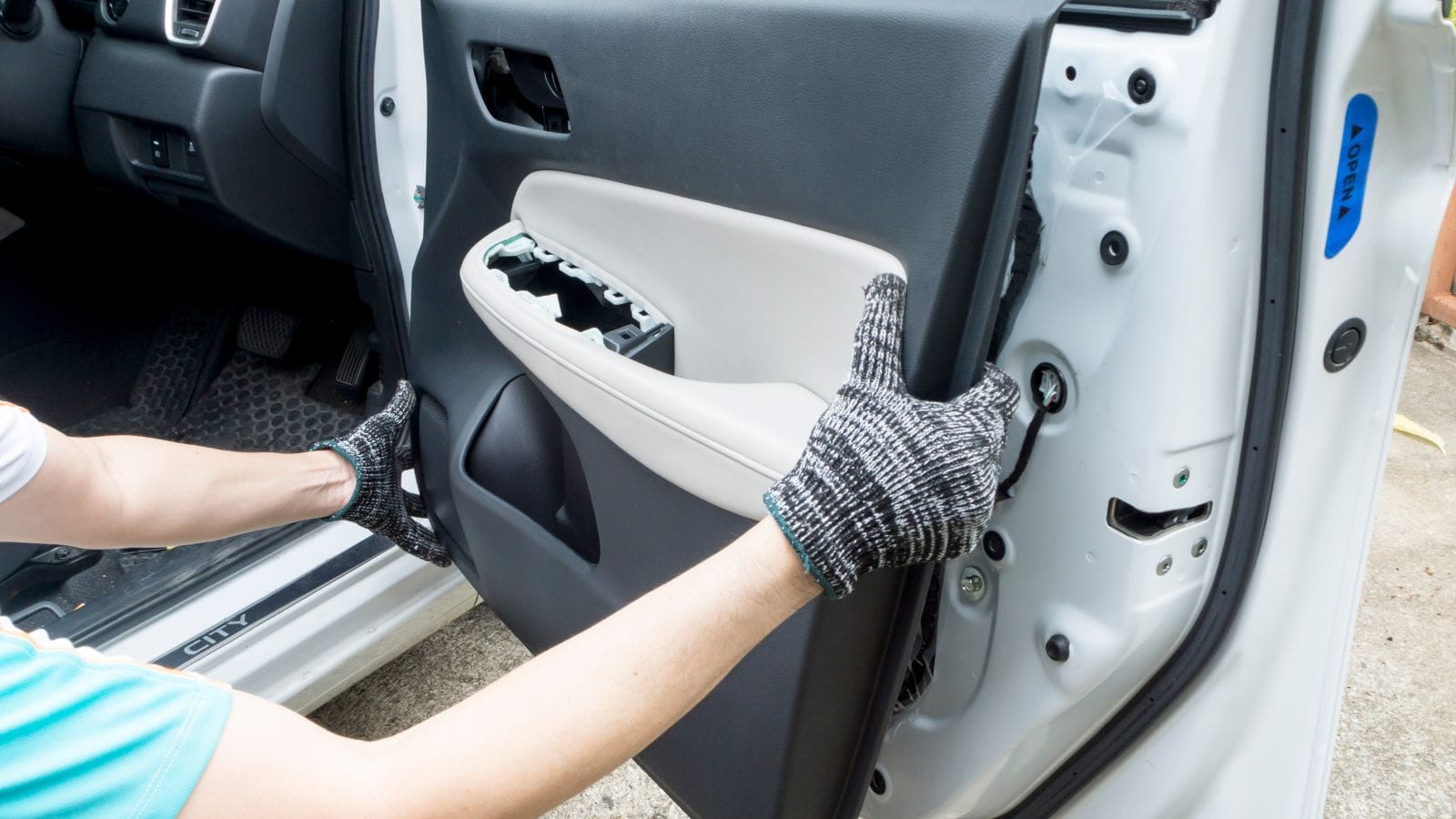
Cambro produces interior trim and specialty plastic parts for vehicles. The company sources many materials from overseas, making it sensitive to tariff fluctuations. Rising resin and additive costs have forced Cambro to rethink supply agreements and adjust pricing. Production delays linked to customs inspections have also become a problem. Despite these challenges, Cambro focuses on quality and innovation to meet growing automaker demands. The company is cautiously optimistic but aware that ongoing tariff battles could impact long-term growth and investment plans.
Metalsa Canada (Burlington, ON)
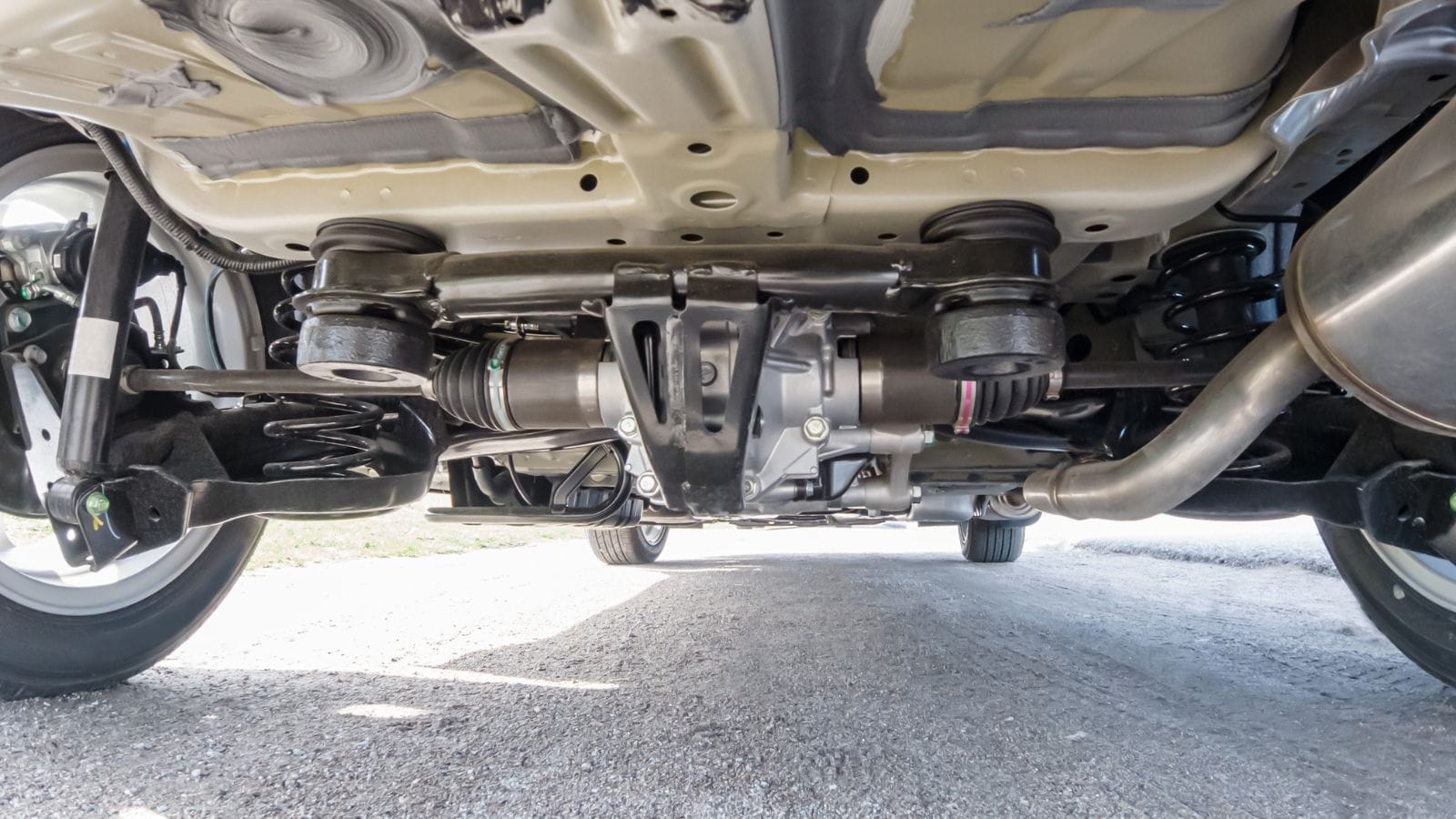
Metalsa manufactures structural components like frames and chassis parts. Tariffs on steel and aluminum have significantly increased input costs. The company has responded by negotiating with suppliers and exploring new sourcing options. Increased production expenses have made contract negotiations with automakers more difficult. Still, Metalsa is investing in automation and lean manufacturing techniques to offset these pressures.
Superior Plus (Calgary, AB)
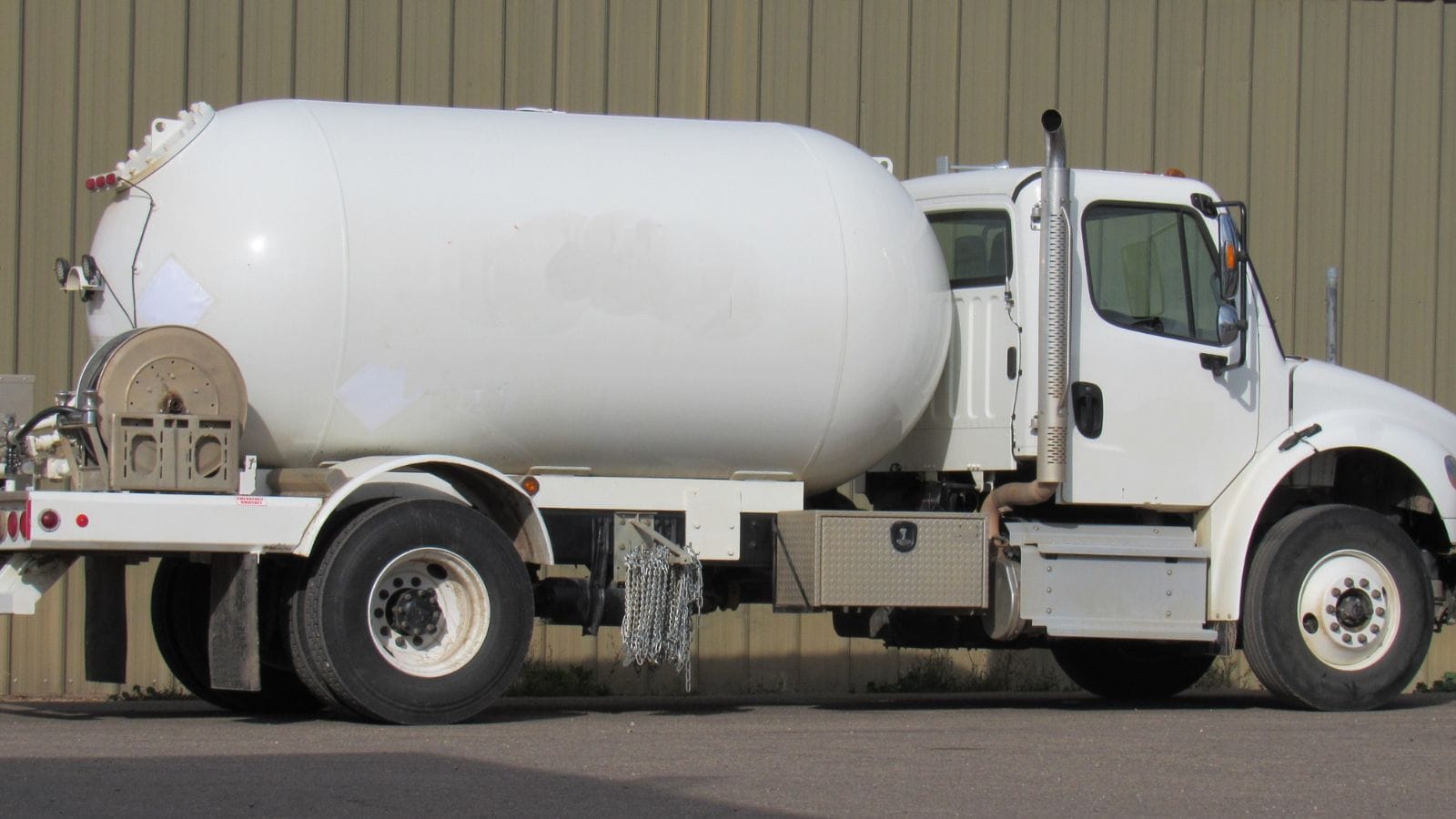
Superior Plus supplies propane and related services to manufacturing plants, including the auto sector. Although not a parts maker, the company feels tariff impacts indirectly through rising fuel and transportation costs. These increases add pressure to manufacturers relying on propane for heating and production. Superior Plus is working to secure stable pricing contracts and improve service efficiency to help clients manage expenses. The ripple effect of tariffs on energy costs shows how trade tensions touch every part of Canada’s automotive ecosystem, making resilience essential across the board.
22 Times Canadian Ingenuity Left the U.S. in the Dust
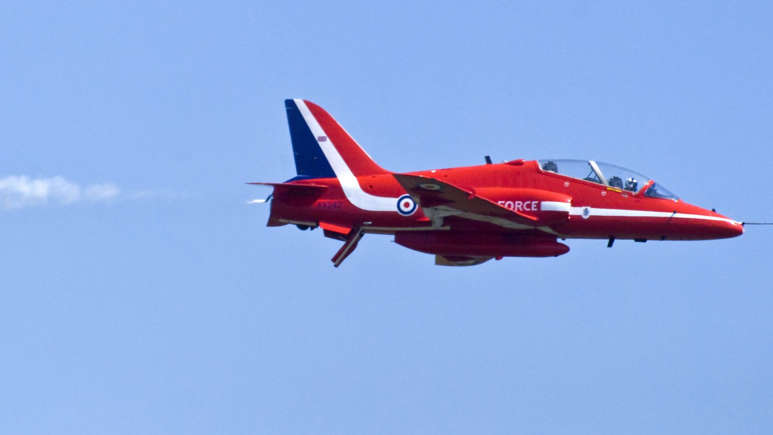
When people think of innovation, they often picture Silicon Valley. However, Canada has a history of innovation, too. Whether it’s redefining sports, revolutionizing medicine, or just showing America up at its own game, Canadian inventors, thinkers, and dreamers have had their fair share of mic-drop moments. Here are 22 times Canadian ingenuity left the U.S. in the dust.
22 Times Canadian Ingenuity Left the U.S. in the Dust
